3D scanning to revive the Audi Sport Quattro legend
The Audi Sport Quattro road and rally car has delighted many car enthusiasts since it was first launched some 40 years ago. Some even call him a “motorsport legend”. LCE Performance and Downforce Performance, both motorsport enthusiasts, decided to recreate the Audi Sport Quattro using 3D scanning.
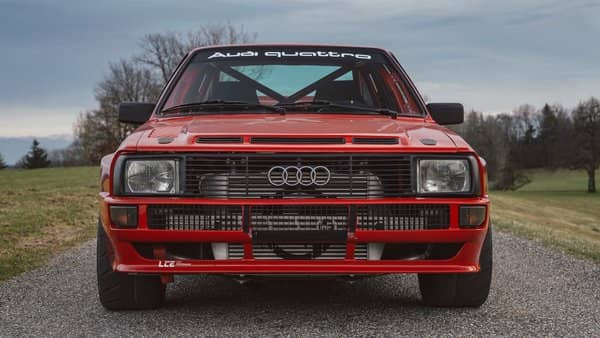
LCE Performance, with its long experience in car adaptation and engine technology, led the project, while Downforce Racing offered its carbon part development services.
The teams worked together to reproduce the Audi Sport Quattro with carbon parts and CFD simulations. Their replica of this legend looks absolutely stunning!
MAIN CHALLENGES
The main challenge in this project was to obtain original parts, as most of them are no longer available. Many of the original parts are no longer in production, as this is an old example. Even if second-hand parts were available, they were expensive to buy or needed refurbishment.
One LCE Performance employee said: “They are 40 years old and look desperate. I can hardly even renew them.”
For a company that wants to focus on providing high quality and durable parts to its customers, these poor second-hand parts were not an option.
3D SCANNING WITH FREESCAN UE PRO FACILITATED REPRODUCTION OF PARTS
This challenge can be solved in two ways using 3D scanning technology. The first is to replicate a new part by scanning the original, and the second is to 3D scan the race car and develop the design from scratch.
In this case, LCE Performance decided to 3D scan the entire body of the car. The team used
Shining3D FreeScan UE Pro
. Before 3D scanning the chassis, the fenders and other accessories were removed to make it easier to get a “clean” 3D or CAD model.
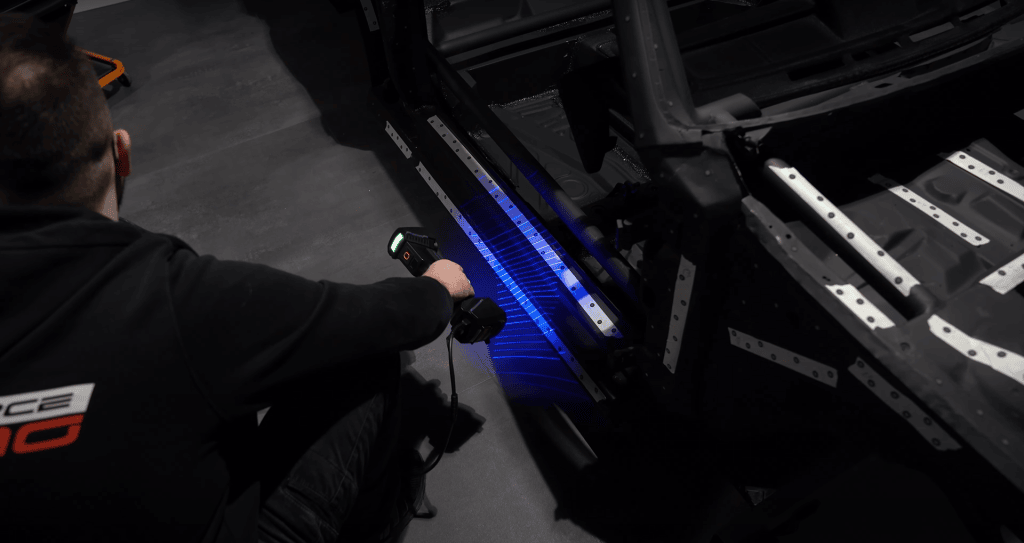
The entire body of the car was then scanned to determine whether the main geometries of the vehicle were intact or had been damaged in a potential accident.
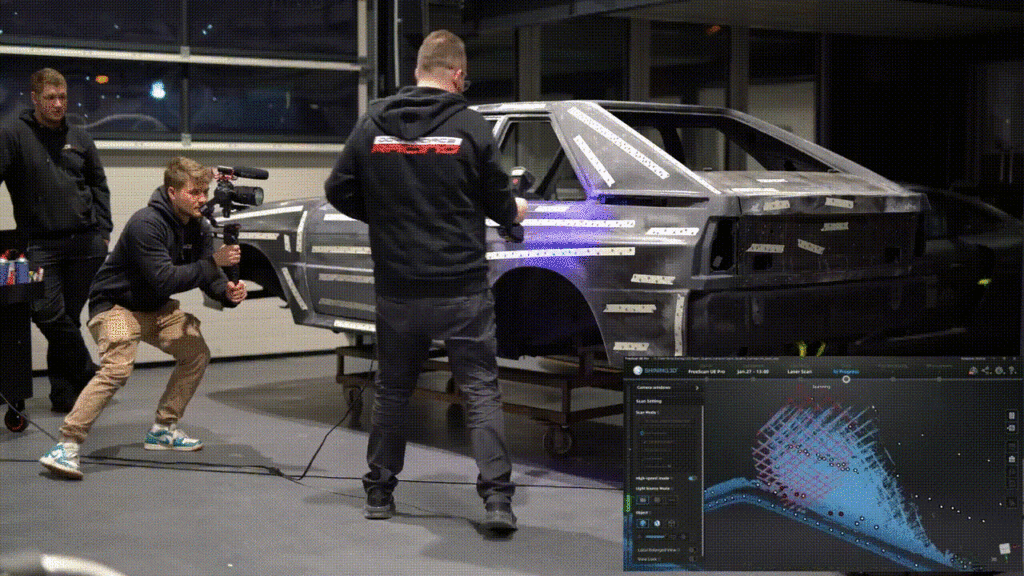
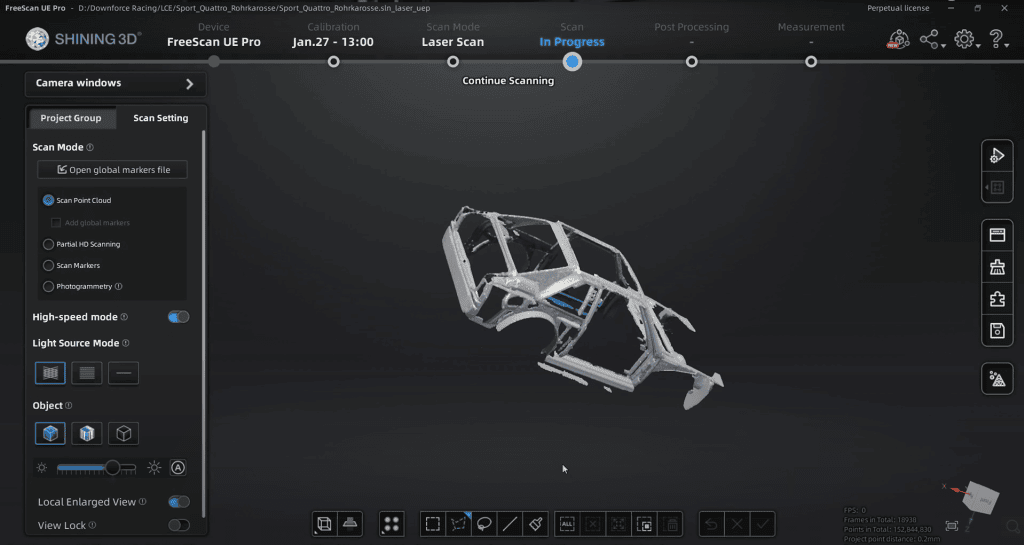
3D SCANNING OF DIFFERENT SURFACES
Using 3D Quick Mode FreeScan UE Pro’s Rapid Mode scanning enabled the team to easily and quickly acquire high-quality data, even on such a large object. In addition, they did not need to spray on the dark carbon parts. However, they had to do the latter to scan transparent surfaces such as windows.
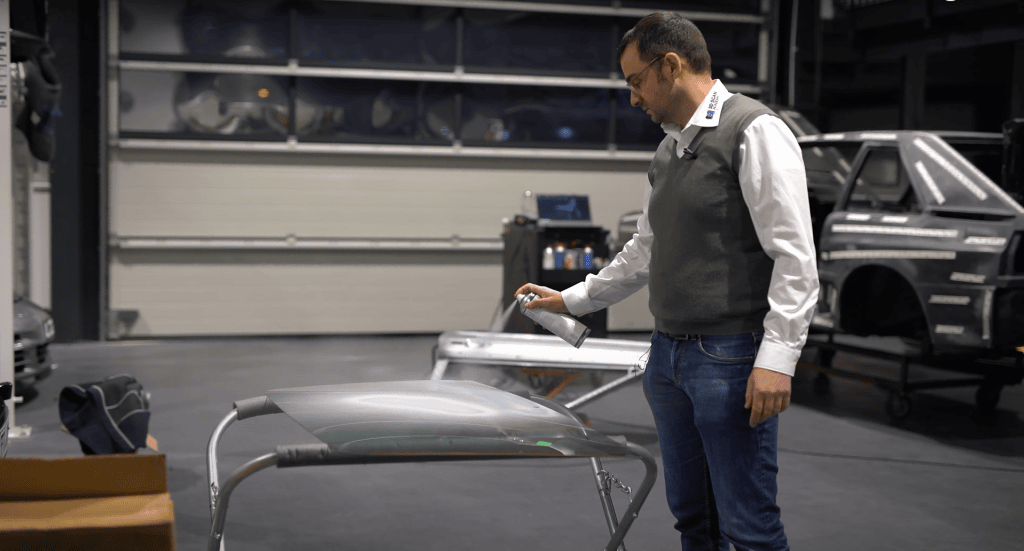
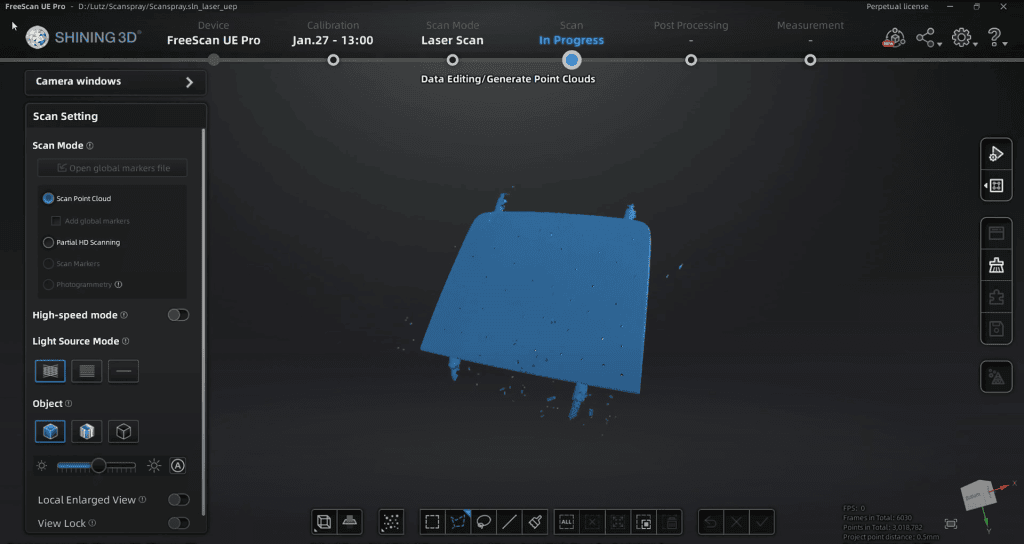
3D SCANNING AND CAD MODELLING FOR CFD SIMULATIONS
After the 3D scan, it was time for the engineers from Downforce Racing to enter the scene. The parts were created using accurate 3D data provided by LCE Performance.
S procedure
reverse engineering
some of the 3D models obtained from 3D scanning were refined and used in CFD simulations to improve the car’s performance. CFD is a simulation tool used to analyse and predict the behaviour of fluids and gases in motion. Using CFD simulations, the team was able to test and optimise the design of the new carbon parts before they were produced. This allowed them to improve the car’s aerodynamics and reduce drag, resulting in better performance every time.
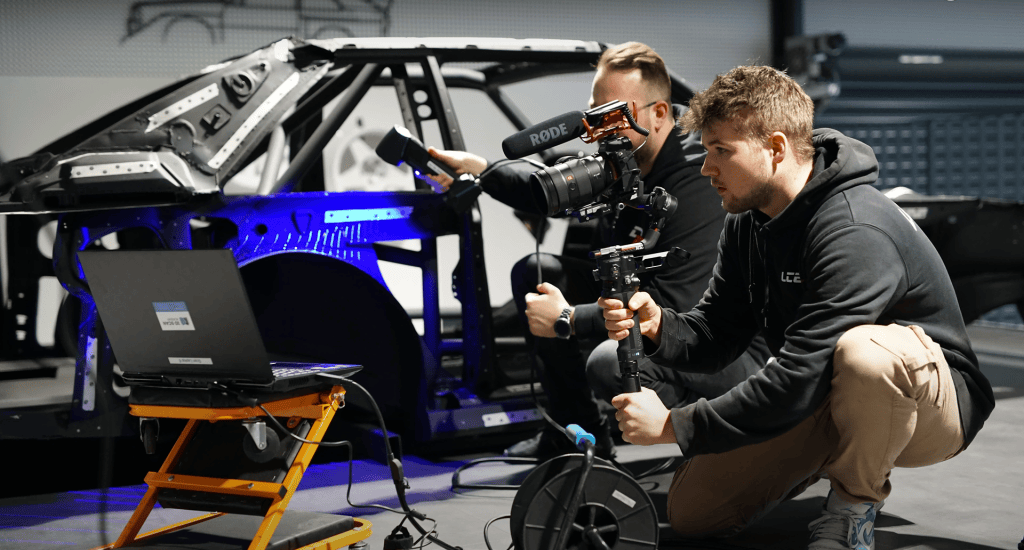
The success of the collaboration between LCE Performance and Downforce Racing is partly due to the efficient use of 3D scanning technology. This demonstrates the invaluable role of 3D scanning in the field of racing cars, especially in overcoming challenges such as accurately reproducing parts and improving the performance of racing cars.