CAM programming of wheel components with hyperMILL
Kettenreaktion Bikes
is a German company that produces lightweight, high-tech and fully customised stainless steel frames for gravel bikes. In addition, they also produce some milled bicycle components such as handlebar and gearbox mounts, crankcase, sprockets and brake discs. They use 5-axis milling machines and hyperMILL CAD/CAM software from Open Mind Technologies.
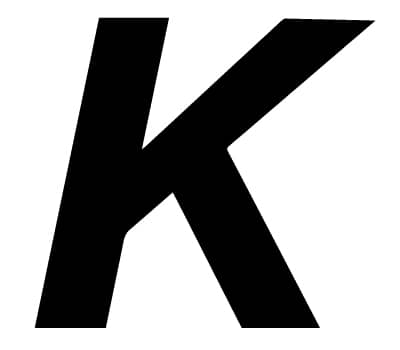
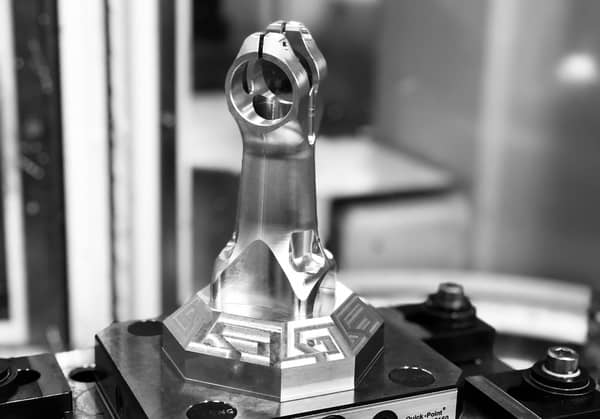
AREN'T STAINLESS STEEL FRAMES HEAVY?
"No, not at all. There is a perception that steel frames are heavy, which is wrong. A stainless steel frame for a racing or gravel bike weighs 8 to 9 kilograms and absorbs vibrations better than a carbon frame. This is very important for ambitious recreational riders who spend a lot of time on the bike."
Marc Gölz is an expert when it comes to bikes. During his professional career, he had long dreamt of designing and building his own bicycle. He got in touch with his friend and cycling colleague Marc Schneider, who is the owner and managing director of a small company called Precimo GmbH. The latter specialises in high-precision milling of complex components made of aluminium and various types of steel. For these purposes, they use one 3-axis and two 5-axis milling machines, and
hyper
MILL
for CAM programming.
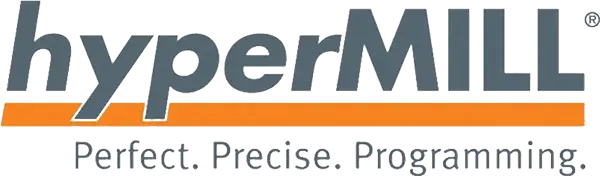
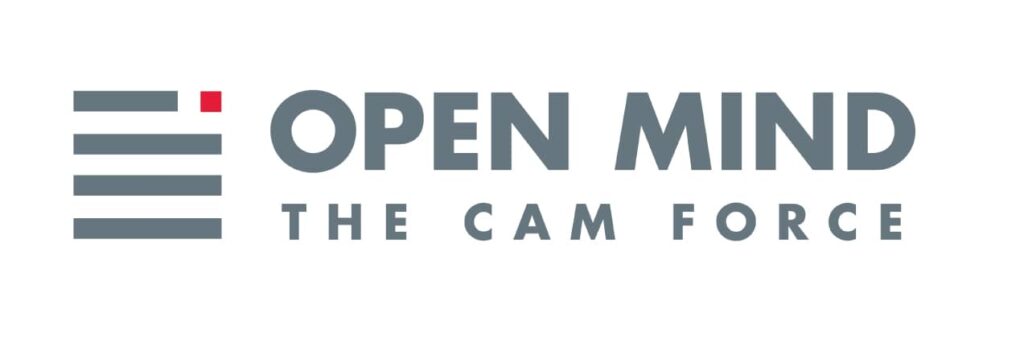
Marc Schneider says: “I believe that
hyper
MILL
is the best software for 5-axis milling. The MAXX Machining module has enabled us to speed up roughing operations and to be able to use the full length of the tool blade. In addition, the “Feature & Macro” technology has helped us to significantly reduce CAM programming time. Last but not least, the ‘Soft Overlap’ function has greatly improved the surface quality in the transition areas.”
"There are several reasons why we decided to develop a high-quality gravel bike with a steel frame. Firstly, stainless steel is gaining more and more fans in the cycling world. This is partly due to the retro trend, as all the top riders in the Tour de France rode bikes with stainless steel frames. Durability also plays an important role, as steel parts are quite easy to modify, repair and recycle. In addition, modern manufacturing techniques give us more options than we would have had 25 years ago when it comes to designing stainless steel bikes."
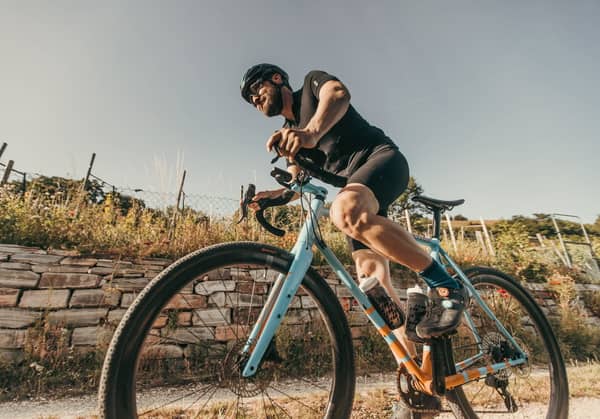
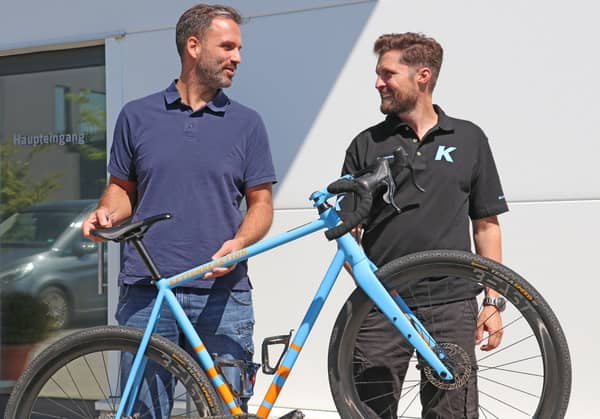
WHEEL FACES WITH COMPONENTS ARE PROGRAMMED IN hyperMILL
This year, Kettenreaktion Bikes will launch more than 20 custom-developed and custom-built bikes to meet the needs of its customers. The founders point out that their company sources 95% of all semi-finished products and components from Germany and Italy. In cooperation with Precima, they also produce as many stainless steel and aluminium parts as possible themselves. Given the current supply problems, they are confident that they are on the right track.
The prototype for the first bike in Kettenreaktion Bikes has been finished for some time. There is also a gravel bike, custom-built for Marc Gölz. This former professional mountain biker is currently testing it. He says he really likes the stainless steel frame. This fully rigid bike uses steel to absorb all vibrations, which is particularly good for the spine.
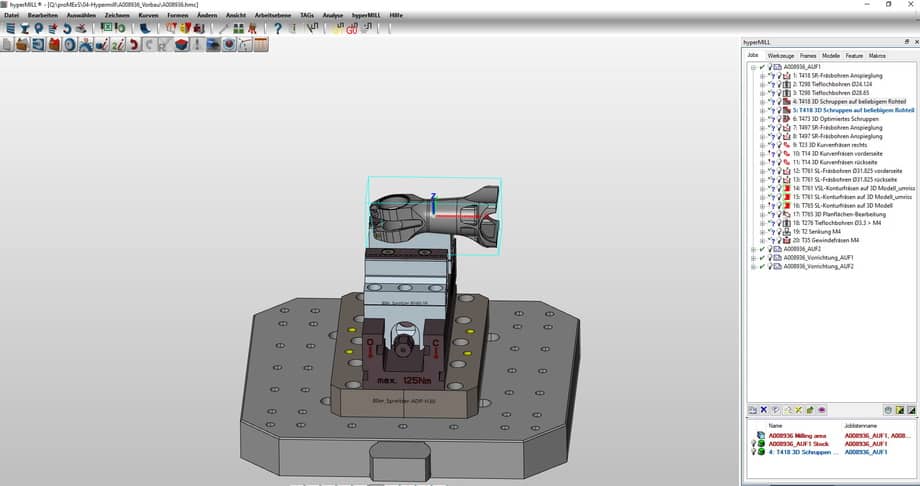
The length of the hose is adjusted according to the length of the rider’s legs and arms, position, etc. This is not possible with carbon wheels, as the frame is always made in fixed shapes. Components such as the rudder bracket are quite difficult to manufacture. It was produced on a Hermle C 22, a high-performance 5-axis machine. The NC programme was of course designed with
hyper
MILL
CAM software.
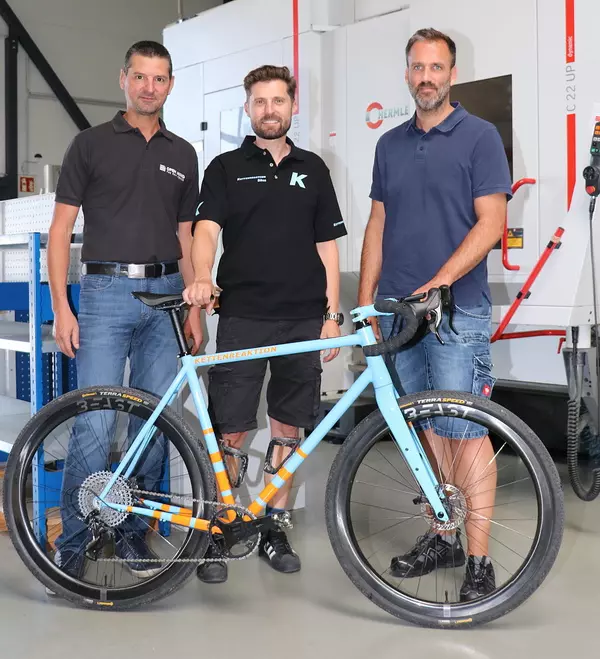
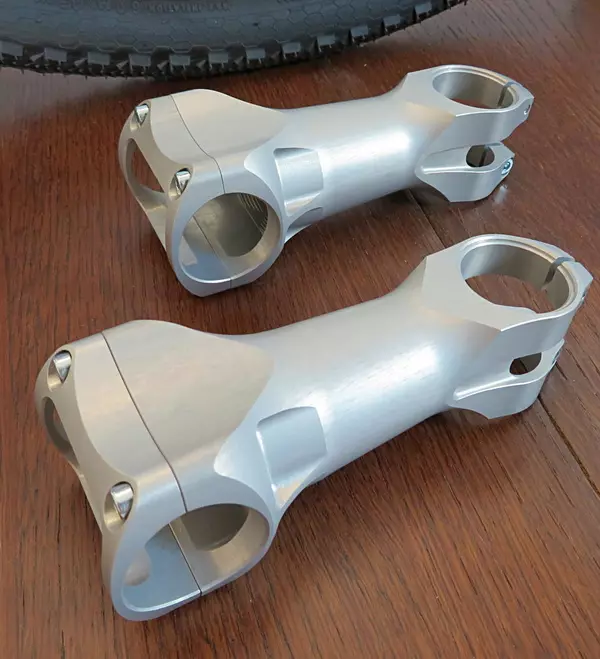
Other components developed by Kettenreaktion Bikes and milled by Precimo include the crankcase, cranks, seat clamps, sprockets and brake discs. Marc Schneider points out that all the parts are designed in-house and are not cast, but milled from raw material.
hyper
MILL
allows each milling path to be determined individually. This has led to a special service – they can engrave the customer’s signature on the handlebar carrier.
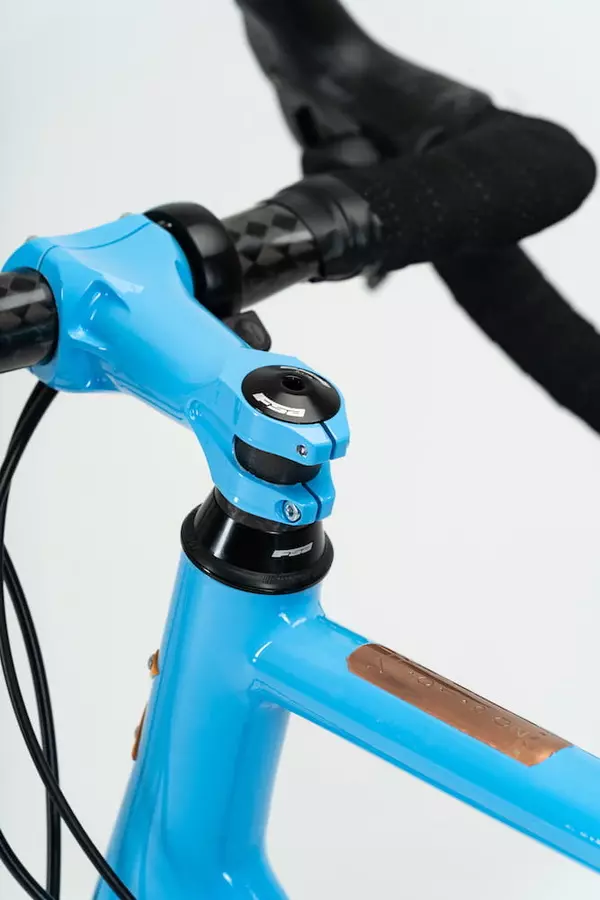
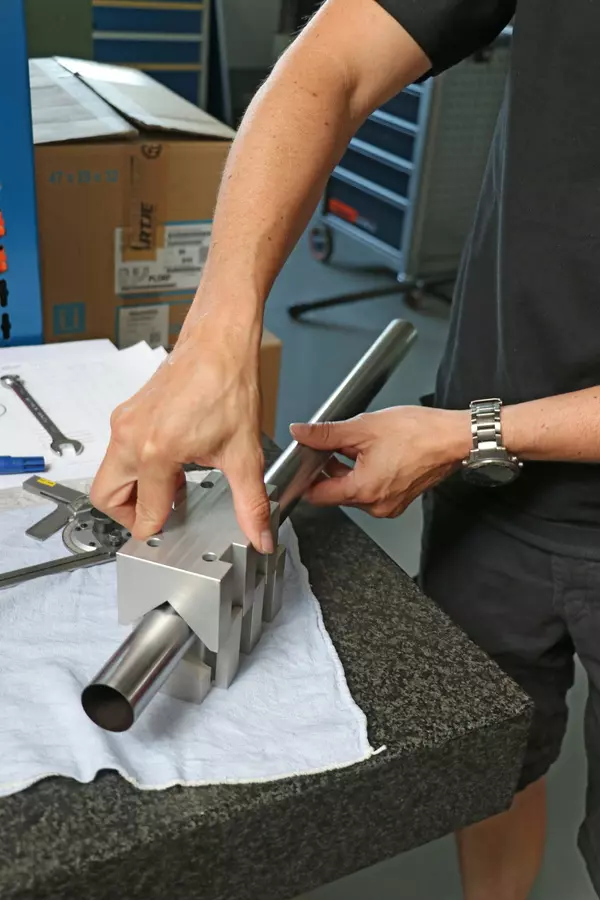
All this means that Kettenreaktion components cannot be copied in any garage. This is very important for Gölz and Schneider, as they intend to sell components that can be used on most gravel, mountain, racing and other bikes as stand-alone parts. Customers can then use them to upgrade and customise their current bikes.
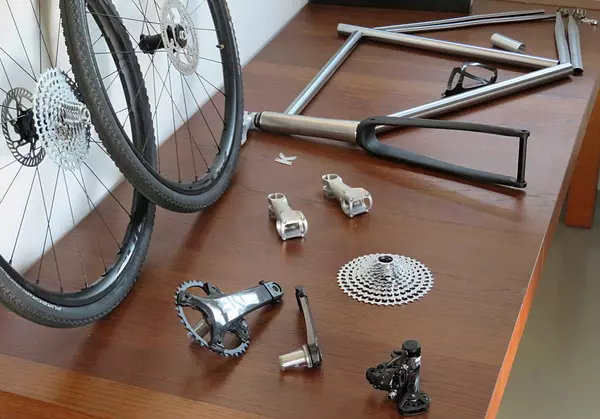
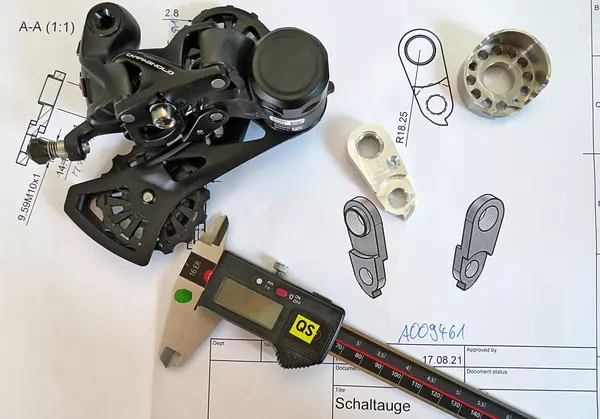
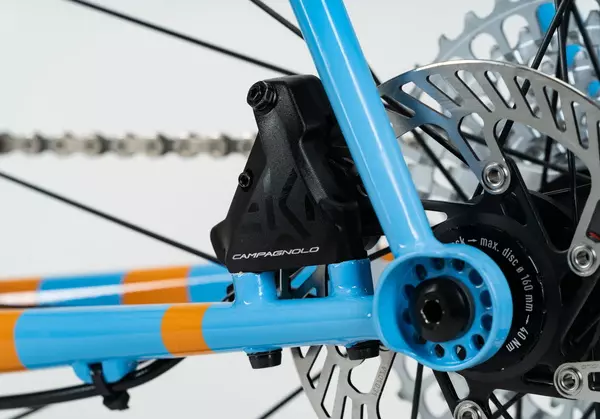