STIHL – Faster Programming, Faster Milling
CNC Manufacturing in the Pre-Production Series and Services department at STIHL has been using the hyper MILL CAD/CAM system from OPEN MIND for the past two years. This had led to an increase in efficiency. In addition to the fast programming of the 5-axis machining centers, the main contributors to this increased efficiency are the hyperMILL VIRTUAL Machining module and the BEST FIT function. This function makes it incredibly easy to align the components and ensures a precise milling process.
In the department for pre-production series, the created prototypes and services at STIHL have been using the hyper MILL CAD/CAM software from the German company Open Mind Technologies for the last two years. Using hyperMILL has helped to increase efficiency. The “Virtual Machining” and the “Best Fit” function in hyper MILL contribute the most to fast 5-axis programming. Itenables easy alignment of components and ensures a precise milling process.
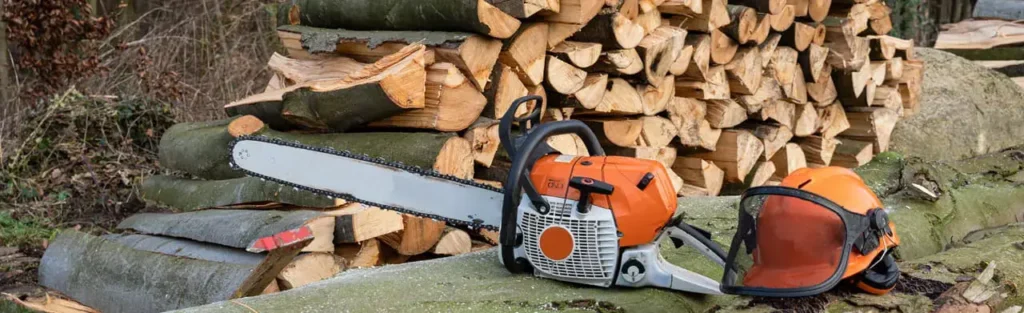
THE STIHL COMPANY AND PROGRAMMING WITH hyperMILL
All forestry workers are familiar with STIHL chainsaw devices based on their characteristic orange color. Although the Waiblingen-based family business has been the global market leader for chainsaws since 1971, the company has much more to offer including numerous tools for sawing and cutting, mowing and planting, cleaning and tidying.
The motivation for the company is – as can be read on their homepage – “to make it easier for people to work with and in nature.” A strong culture of innovation is cultivated to create added value for customers with new technologies. This is why the competence and development center at the headquarters in Waiblingen, Germany, is so important. More than 700 developers work together here across disciplines.
Prototypes, small batches, and initial samples are created in the “Additive and CNC Manufacturing” team. The parts and components created in the design and development department are made from aluminum, magnesium, steel, brass, and plastic. They use them to test their prototypes, which are the basis for new products. This means that their team has to be very flexible and quick in different manufacturing tasks in order to keep the time for initial functional tests as short as possible.
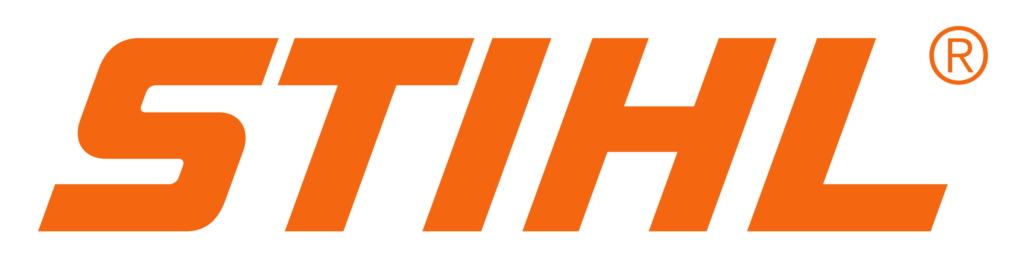
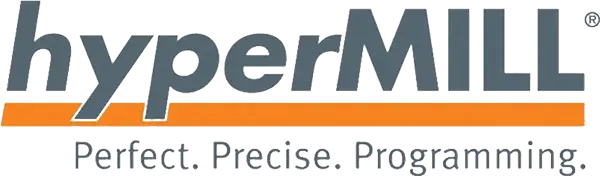
Where possible, the components are machined by milling or turning. State-of-the-art equipment is available for milling, including two 5-axis simultaneous machining centers, three 3+2-axis milling machines and one multi-axis wire EDM machine.. When the geometry of components is unsuitable for milling, they use additive manufacturing. Laser Beam Melting for processing meatal powders and Selective Laser Sintering for polymer parts These additively produced parts usually require postprocessing, such as NC machining in order to ensure the required functional dimensions and surface qualities.
"The investment in hyperMILL has definitely paid off. Programming efficiency has increased and we have achieved significantly higher machine utilization. As a result, we are currently expanding the use of the software so that we can also run it on other machines."
NO MORE BOTTLENECK NC PROGRAMMING
5-axis machining for small batches and prototyping represents an ideal technology, as it can usually lead to a finished component in just one clamping. The basic requirement for this is a workable, process-reliable NC program.. “This has been a bottleneck for us in the past,” says team leader Matuschka. “Programming with the previous system required more time, which meant that we had to use additional external service providers in case of overcapacity.”
The decision was made to use a new CAM system, so the responsible team started to search for the optimal CAD/CAM solution. Four systems made it into the pre-selection, and two of them went into the extensive test phase.
“The hyperMILL CAM system offers an extremely innovative “Automatic indexing” function for 5-axis programs. This allows to divide a 5-axis program in single operations with a fixed tool angle. Thereby we were able to translate programs made for our 5-axis machines into programs that are compatible with our 3+2-axis Machines, without a whole reprogramming of the part. OPEN MIND was open to our request and developed an appropriate solution.”
NO MORE BOTTLENECK NC PROGRAMMING
STIHL asked the two remaining CAM vendors to program a benchmark project to get a neutral comparison of the maximum that can be achieved from the two CAM programs.
The task involved milling a crankcase component containing many areas that had to be adjusted or milled simultaneously. Narrow ribbings, which had to be machined with small tools, also posed a difficulty. Using hyper MILL they were able to reduce the machining time and the time required for programming, with the result that STIHL ultimately opted for the hyper MILLsoftware.
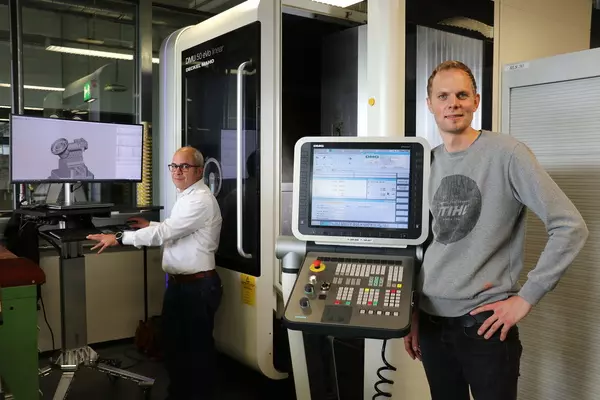
Benjamin Gruber praises the fact that the system is so easy to use. After two weeks of basic training, he was already so familiar with the software that programming 5-axis parts was no longer a problem for him: “hyper MILL offers a large selection of 5-axis functions that can be programmed mostly automatically. This is quick and is a great strength of CAM system.”
"END-TO-END" SOLUTION - FROM CAD TO MACHINE
Up to now the STIHL prototyping department had always needed a range of software solutions such as an extra simulation system and a tool database. hyper MILL now offers everything in one system.
It is the VIRTUAL Machining module within the hyper MILL CAD/CAM softwarethat sets it apart from other systems. In a sense, it is the cornerstone of NC code generation and NC code simulation as well as the basis for various functions.
"BEST FIT" - INTELLIGENT COMPONENT ALIGNMENT
The easy alignment of additively manufactured parts within the machine is particularly important for STIHL.
Benjamin Gruber describes how it used to be: “In the past, we adapted the component and the clamping in the machine to the conditions of the NC program. In other words, we manually added a reference geometry to the part and aligned the zero position within the machine by probing. We had to repeat this process until the alignment could be captured as accurately as possible. This is needed due to bigger manufacturing tolerances in additive manufacturing.”
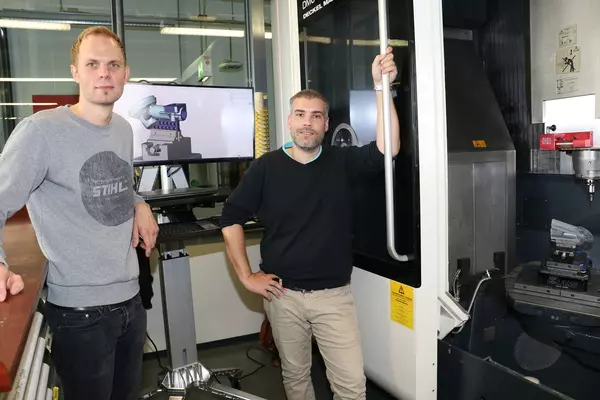
With hyperMILL BEST FIT, real-time alignment takes place directly in the CAM. “We carry out 3D probing of the unaligned component in the machine and feed the probing points back to the CAM system,” explains Benjamin Gruber. “The software takes care of everything else. It adapts the NC-code to the measured part position and virtually shifts the toolpaths to the component. The adapted NC code is simulated in the virtual machine and optimized automatically. To ensure safe and accurate machining, the machine operator gets involved again and performs a verification measurement that checks in the CAM system whether the alignment is within the predefined tolerance. Machining can start after that."
Milling and programming specialist Gruber confirms: “This saves us an enormous amount of time. Thanks to the verification measurement, we can also be sure that the machining will run without collisions and that we will obtain the desired milling result in the end.”
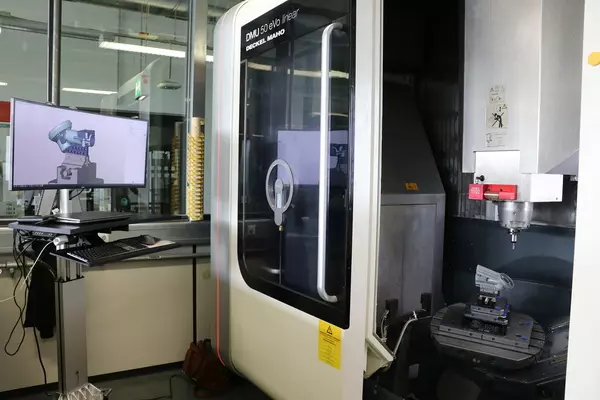
The “Additive and CNC Manufacturing” area of Test Parts Production at STIHL has state-of-the-art equipment at its disposal – a 5-axis machining center and a portable CAM programming station with OPEN MIND’s hyper MILL CAM software.
Matuschka sums up: “The investment in hyper MILL has paid off. Programming efficiency has increased and we have been able to achieve significantly higher machine utilization. This is why we are currently widening the use of the software so that it can also run on other machines.”