The Porsche 991.2 GT3 is even faster with the help of FreeScan UE Pro
Could the already accomplished Porsche 991.2 GT3 be even more powerful? Of course! In collaboration with Ångström Performance, we used the Shining3D FreeScan UE Pro 3D scanner to develop the modified intake pipe for this car’s engine, which helped us capture the geometry of the original piece and its position on the car. Based on the data obtained and using the process of reverse engineering we created a new vent, which will allow this “rocket to breathe with full lungs” and make it even faster.
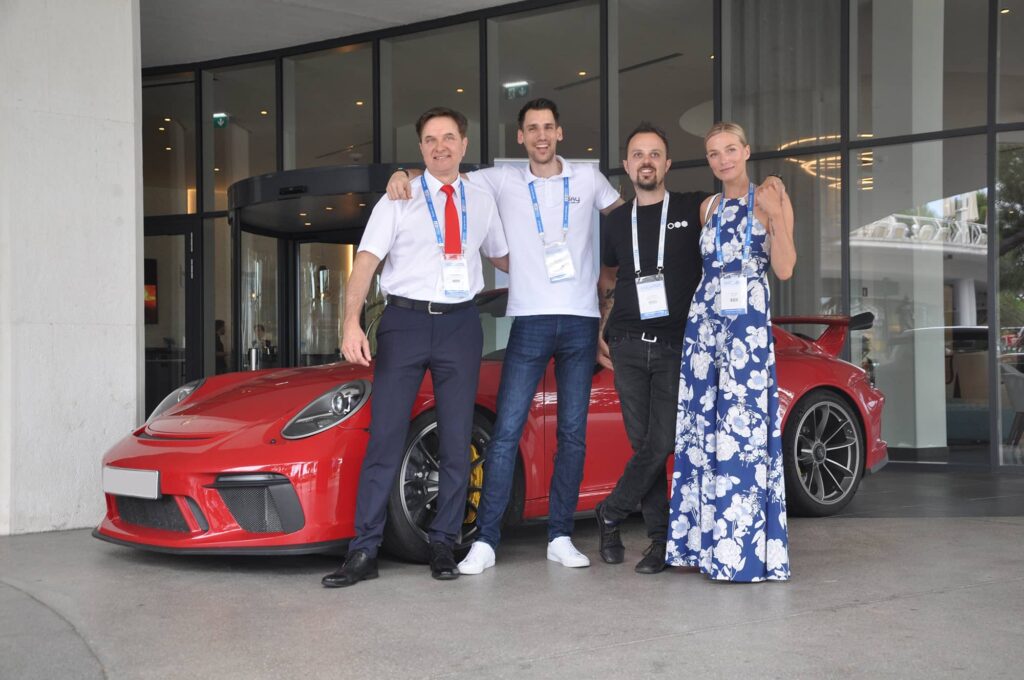
SOMETHING ABOUT THIS SUPERCAR
The Porsche 911 GT3 is a product from Stuttgart. Over 70 years of progress with an unchanged recipe. Porsche is a small company compared to the other sports car giants. In the entire history of the brand, the GT3 is at the highest level of development, a step above it is only the GT3RS and the much more extreme GT2 RS.
For the 991.2 generation of the GT3 series, Porsche devoted most of its time to building the GT3 RS variant, and the GT3 lost some of the most advanced refinements and received quite a few limitations. The main differences between the two cars are in the exhaust system and air intake to the engine.
THE IDEA OF INCREASING THE EFFICIENCY OF THE PORSCHE 991.2 GT3
The owner of the car approached us with the need to solve another part. The purpose of the intake pipe modification for the Porsche 991.2 GT3 car was to improve the performance and efficiency of the car.
There are small but very important differences between the GT3 and GT3 RS models. The main difference in the power unit is in the exhaust system and the air intake system. Both are equipped with a restrictor on the GT3. After eliminating the restrictor on the exhaust, we wanted to improve the air intake.
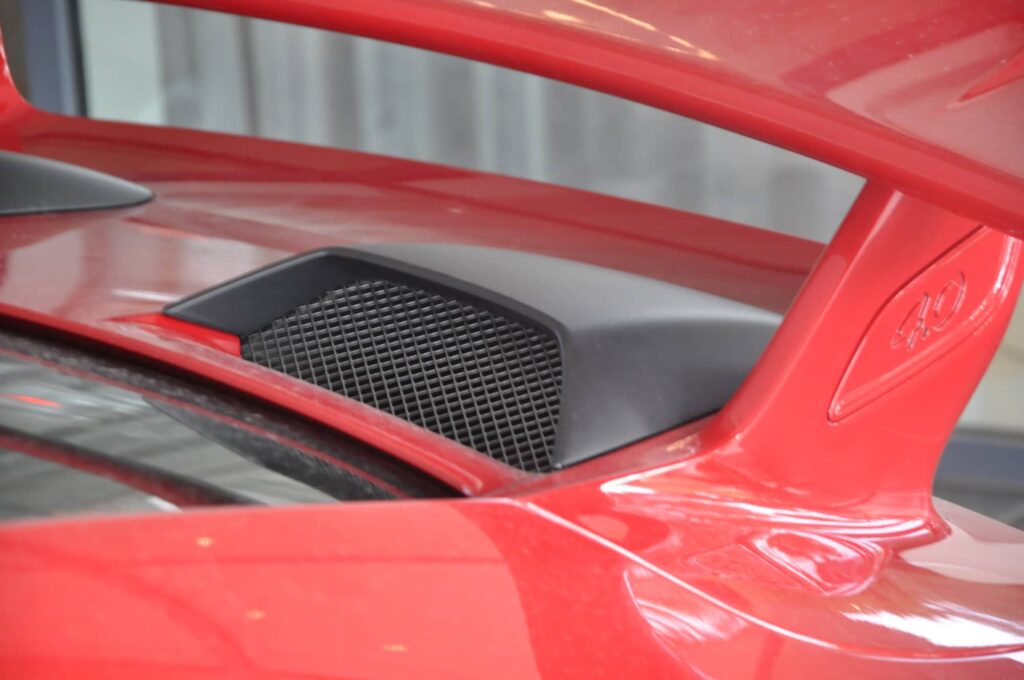
The surface area of the air filter is 207 cm2, and the intake pipes from the cover onwards are of the same dimensions. From the air filter to the inlet, the pipes are reduced to a section of 160 cm2 all the way to the intake covers on the engine cover. Our opportunity was hidden here. Equalizing the intake area to the engine would mean more oxygen for combustion. At Porsche, the engineers used the “RAM air” air supply principle, which means that every square centimeter of surface means a larger amount of air is supplied to the engine. This is of course even more noticeable at higher speeds, where the GT3 spends most of its time on the track.
STEP BY STEP TO HIGHER SPEED…
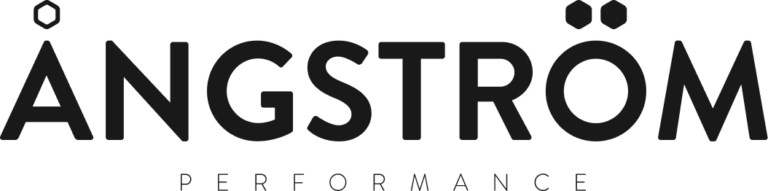
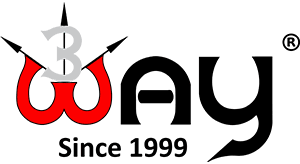
1. 3D SCANNING WITH SHINING3D FREESCAN UE PRO
The first and very important step in the implementation of the project was the measurement. They had to be very precise and fast. It was necessary to cover very complex and hard-to-access surfaces. In 3WAY, we have devices that can do it all – 3D scanners. In this case, we used a 3D scanner from Shining3D, Freescan UE Pro, which belongs to the laser hand-held 3D scanners and has an accuracy of up to 0.02 mm.
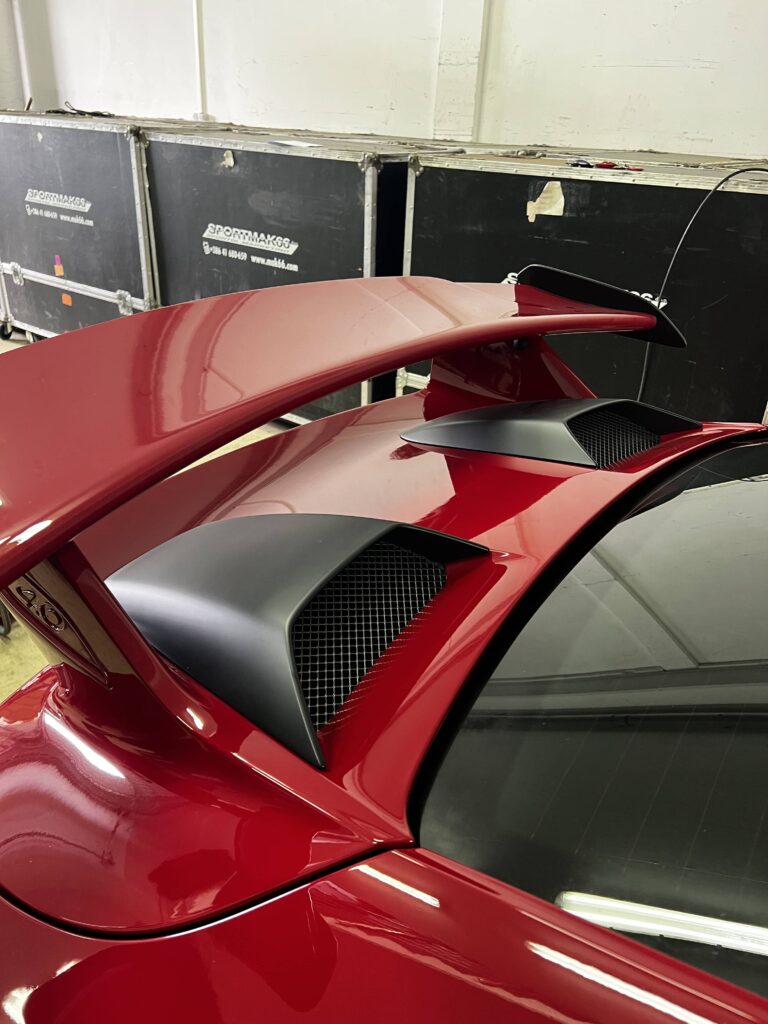
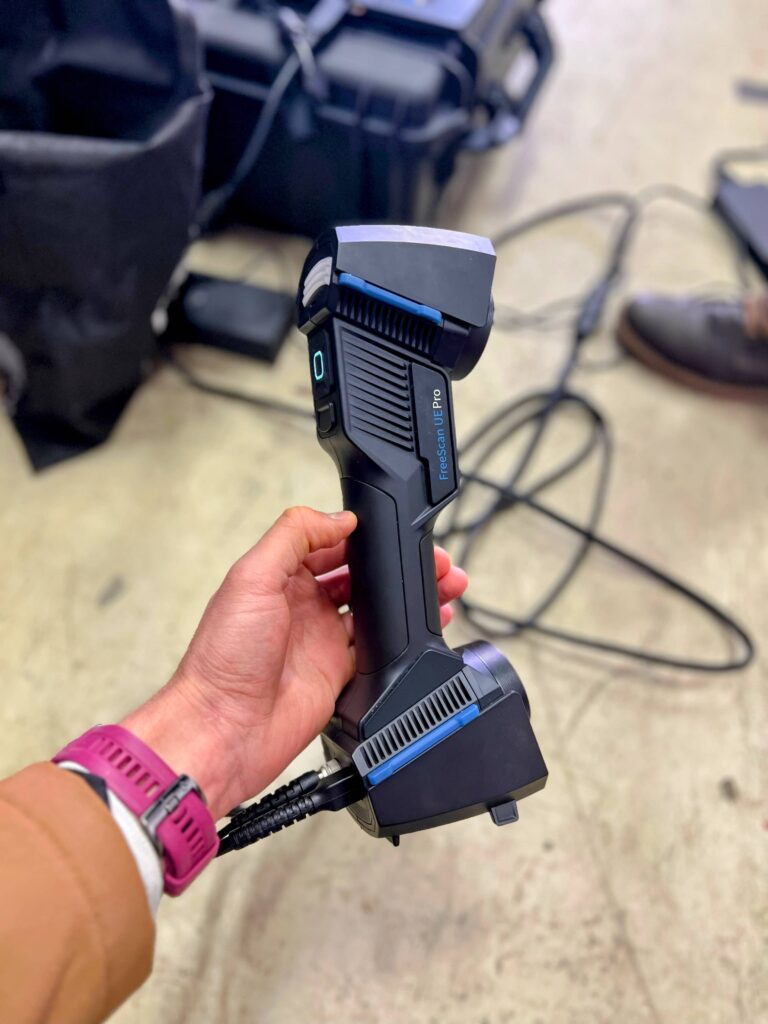
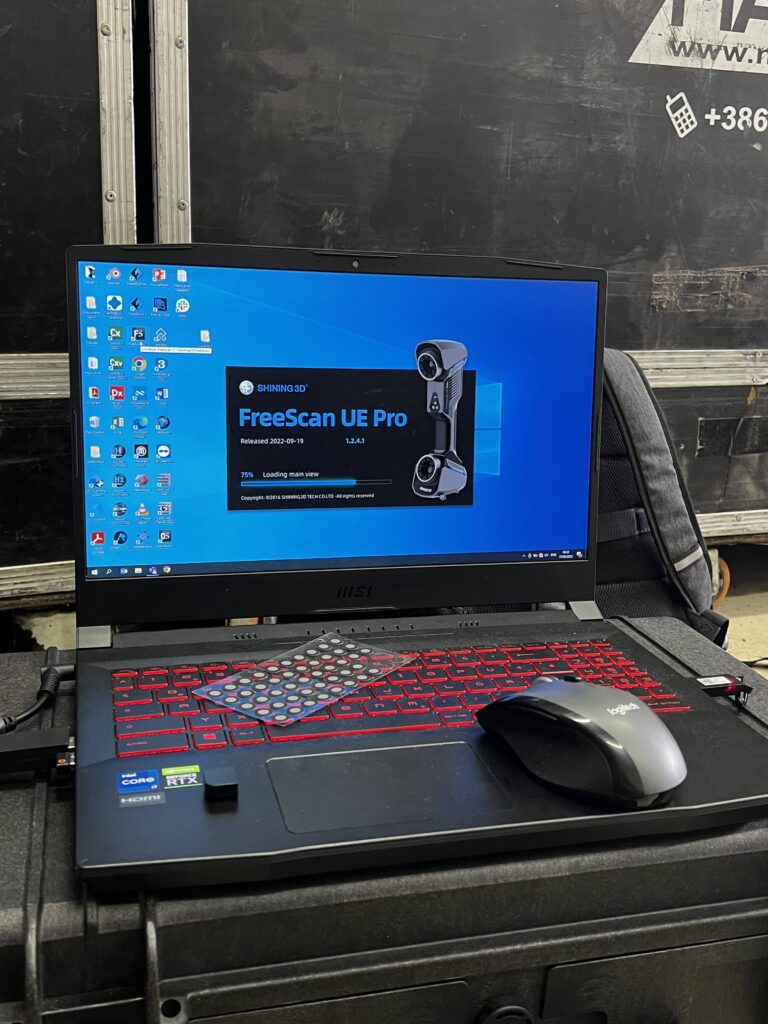
For the proper implementation of the project, it was necessary to carry out several measurements. We scanned the following areas and pieces:
- vent cover in installed condition
- vent cover in its entirety
- inlet pipe in the installed condition
- inlet pipe in its entirety
After completing the 3D scan, we analyzed our measurements and came to the conclusion that the inlet cross-section of the vent shell is smaller than the surface of the air filter. The pipe that joins the engine cover and the engine cover vent is most likely a design bottleneck. The mounting tube has a surface area of 198 cm2. The original cover, which collects air from the surroundings, has a cross-section measuring 152 cm2. Based on the measurements, we developed a plan for the continuation of the project at this location. The goal was to optimize both cross-sections so that the engine gets more positive pressure into the aggregate intake itself at higher speeds.
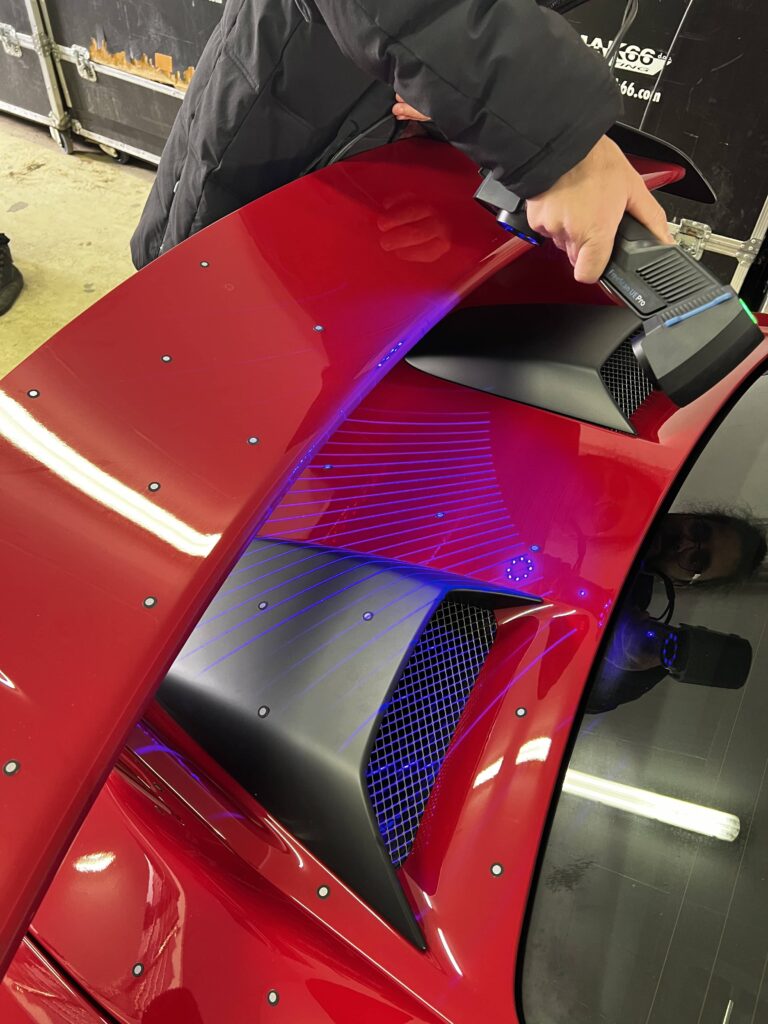
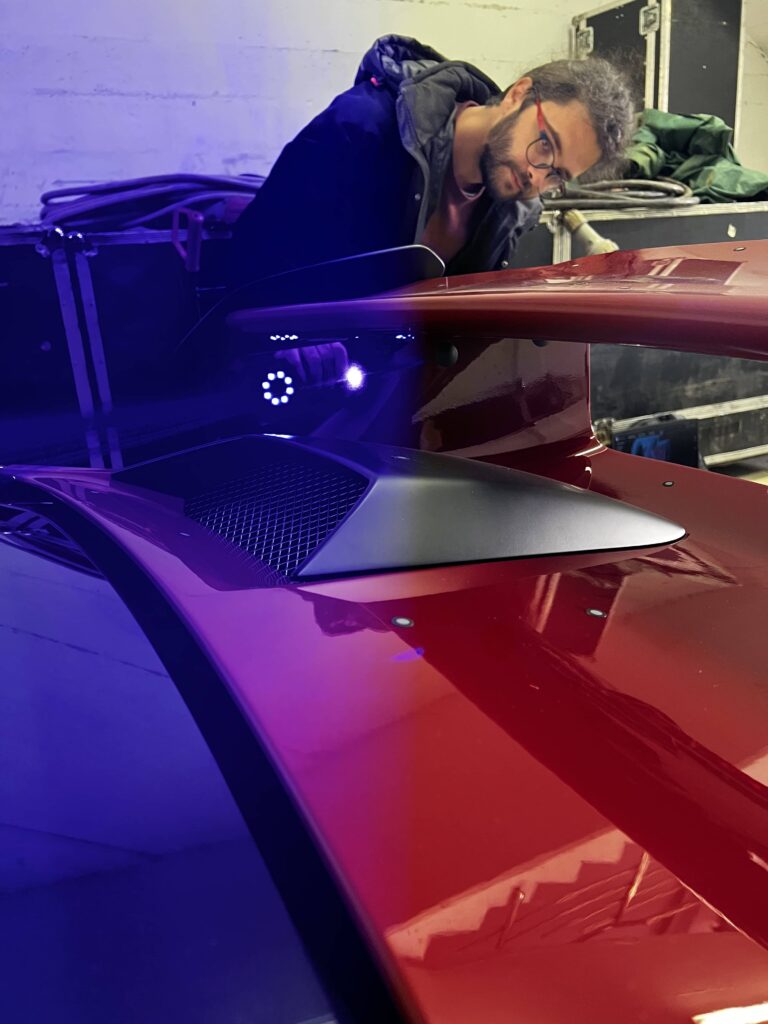
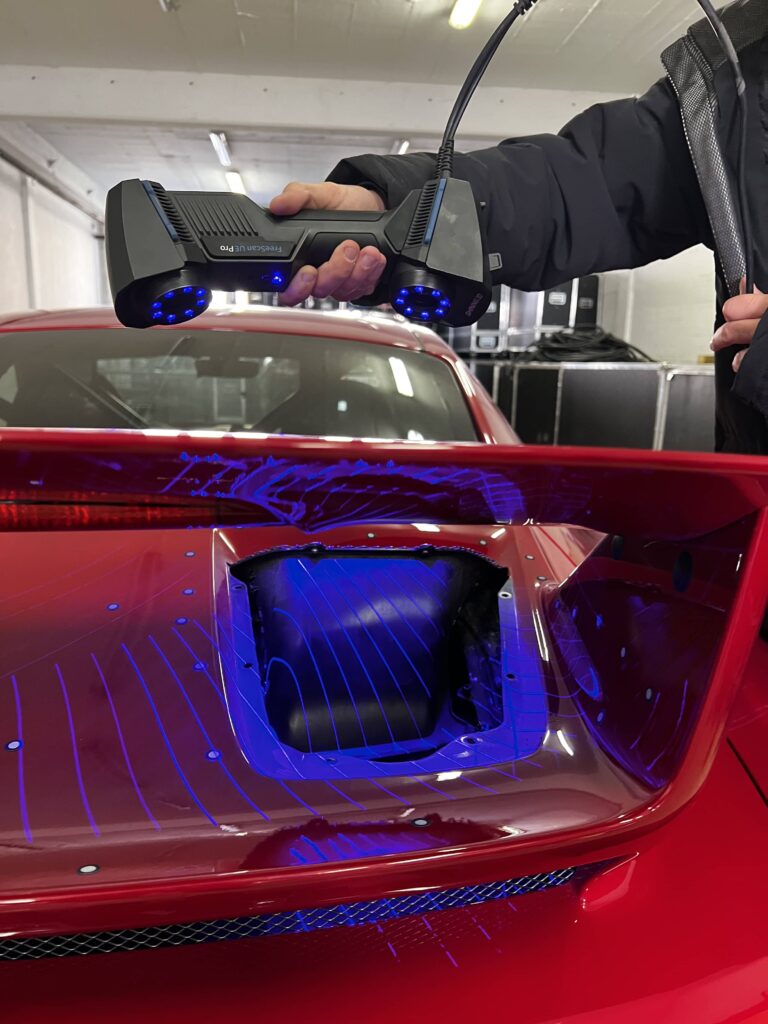
2. REVERSE ENGINEERING WITH GEOMAGIC DESIGN X
Before starting the reverse engineering and the necessary modifications, based on the obtained data, we also performed a CFD analysis (Computer Fluid Dynamics) to calculate the most optimal opening. After calculations, we learned that it is best if the opening has the same or slightly larger cross-section compared to the cross-section of the air filter.
Reverse engineering is a process where we make high-quality surfaces and modifications of existing products based on 3D scans in a 3D digital environment. In our case, we used Geomagic Design X software for this task.
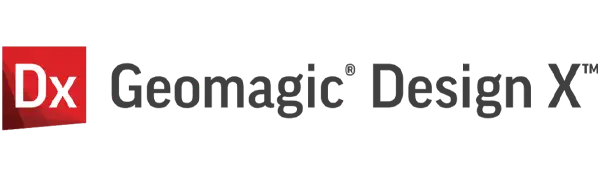
First, it was necessary to align all our 3D scans to each other to ensure a perfect fit. The adjustment of the increase in air intake was necessary in two parts: on the air intake pipe and on the vent cover.
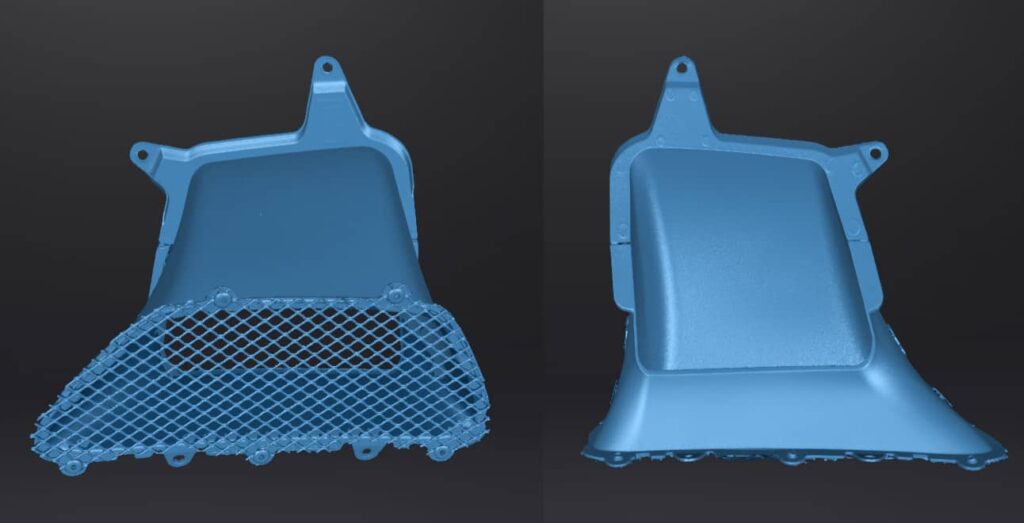
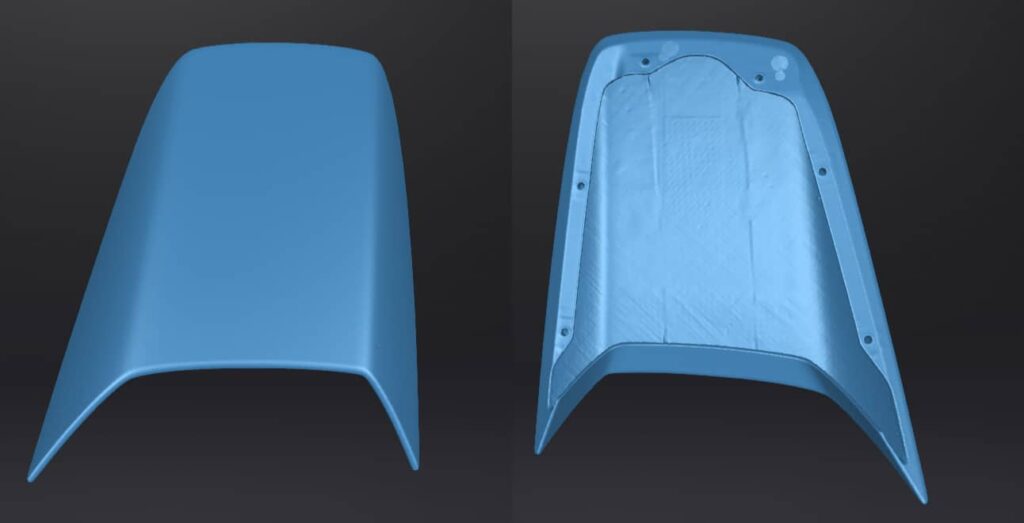
The inlet pipe was made first, as it is much easier to fit the cover afterward. During the actual creation of the 3D model, it was necessary to provide an appropriate cross-section. The inlet pipe now measures 207 cm2, which matches the CFD analysis. This ensured optimal air supply.
In the second part, it was necessary to adjust the vent cover. We ensured a match in the attachment area, and the upper part was changed and raised, where the opening is now larger. Here, the external surface and aesthetics were also very important, as this part is visible and must fit the shape of the car.
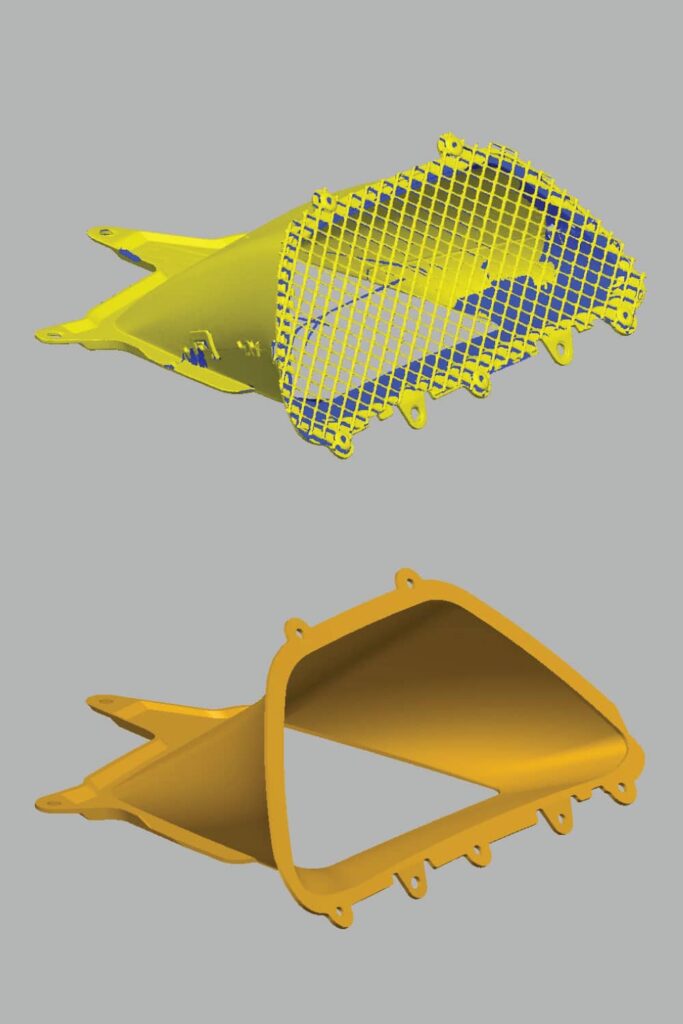
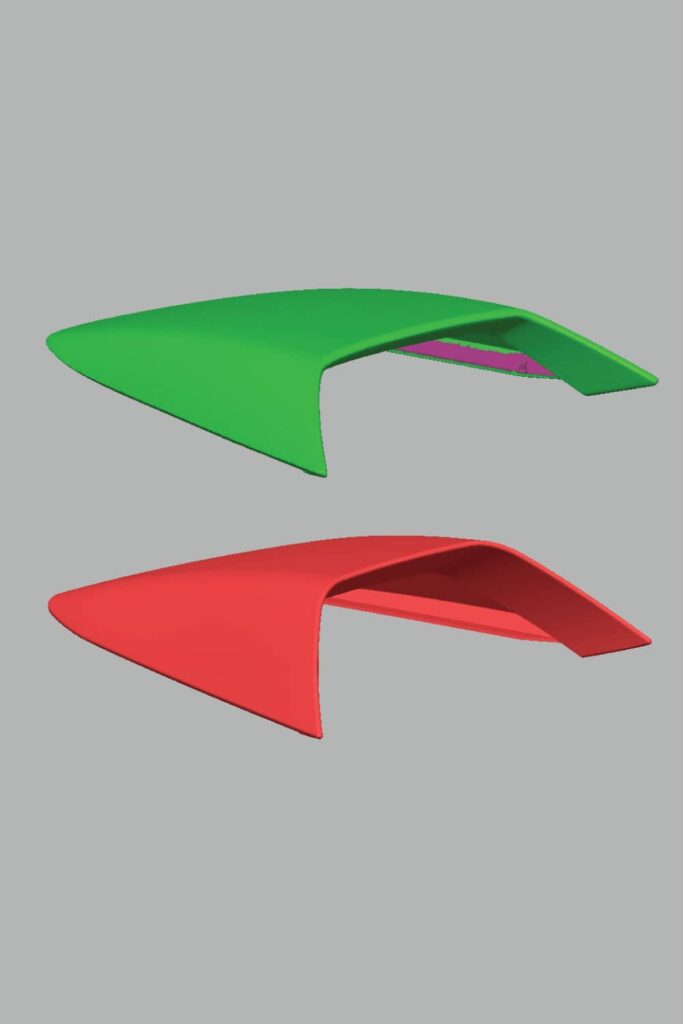
3. MAKING PROTOTYPES USING 3D PRINTING
For the production of prototypes, we needed technology that would allow us to produce parts quickly with low costs. We used FDM (fused deposition modeling) and SLA (Stereolithography) 3D printing technologies to produce prototype pieces. We used an FDM 3D printer to make the inner vent, and the cover was printed with an SLA 3D printer.
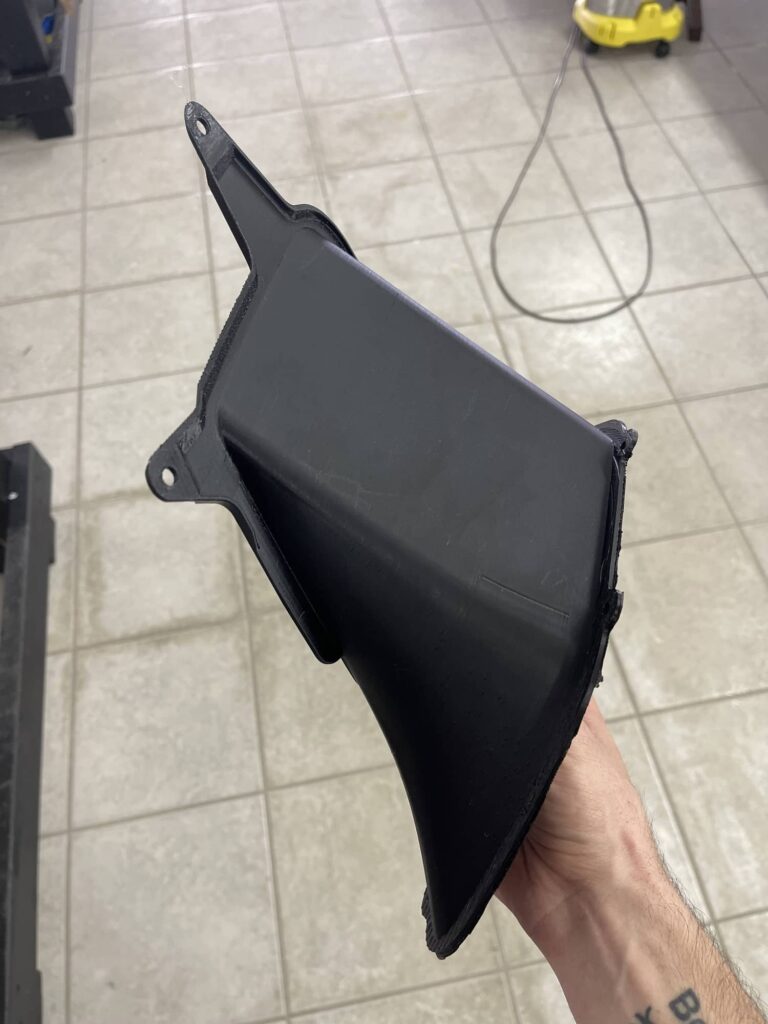
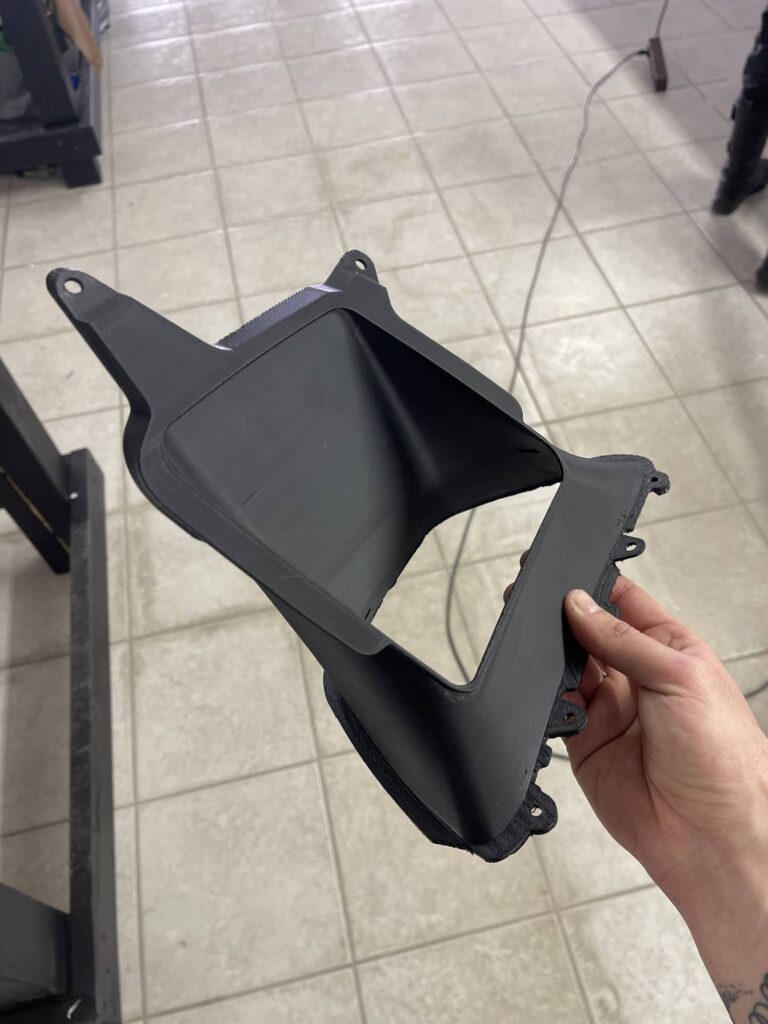
After a few days of applying a layer of epoxy resin and sanding, we made a mold from the 3D printed product.
4. MAKING MOLDS
The molds were made based on the 3D-printed piece. At Ångström Performance, they were made using high-temperature epoxy resin. The carbon fiber was cut using a CNC machine, ensuring that tolerances and overlaps were planned and not approximate. The overlaps between the joints of the pre-impregnated fiber layers are 6 mm, and stainless steel threaded fittings are used to assemble the product. Stainless steel is a much better alternative to other materials because it does not react with carbon fibers.

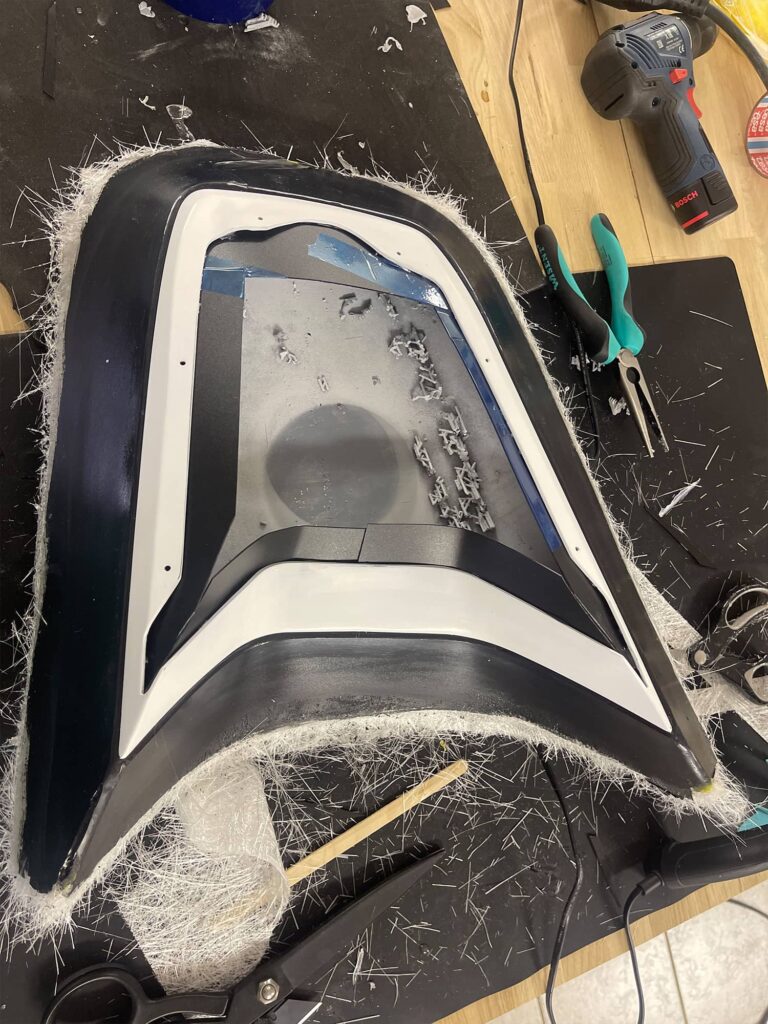
5. FINAL PIECE
We relied to the robots to make the inner shell. We spent much more time on the outer shell, which is visible to everyone. We placed “prepreg XC110” in the finished mold, which we cut with the help of a CNC machine. All seams and overlaps have been planned so that there is as little residue as possible. The joints overlap by 6 mm, which is more than enough for a very solid finished product. The entire top surface of the vent was cast in a single piece. The fibers for the first cosmetic layer were cut to rest at a 45-degree angle to the center line of the car. This visually achieves two air vents, the lines of which direct the eye to the center of the Porsche 991.2 GT3 racing car.
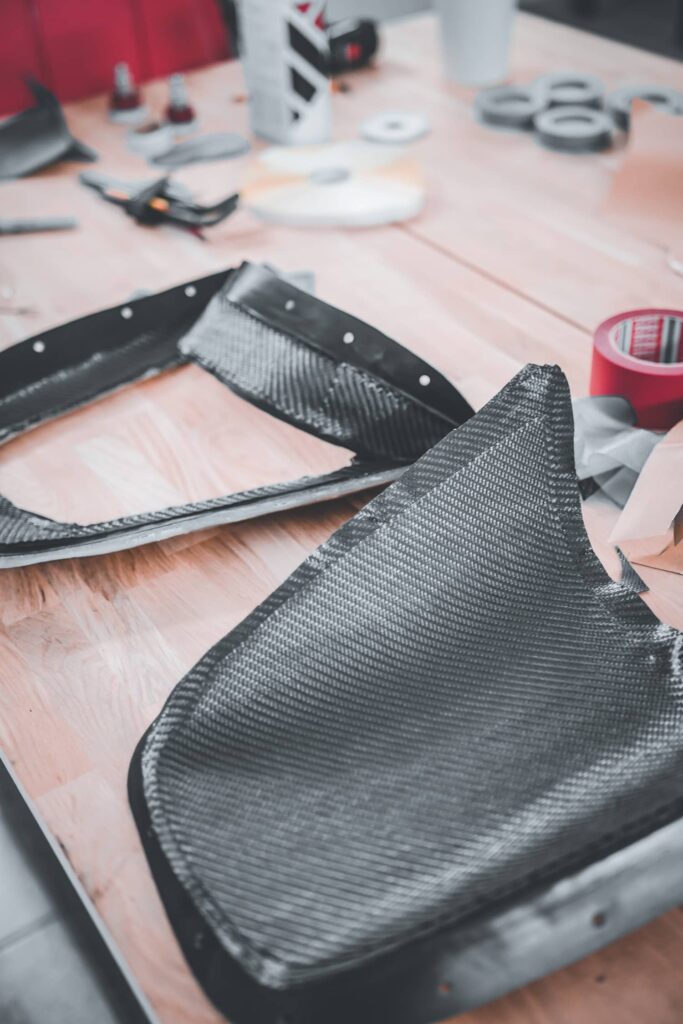
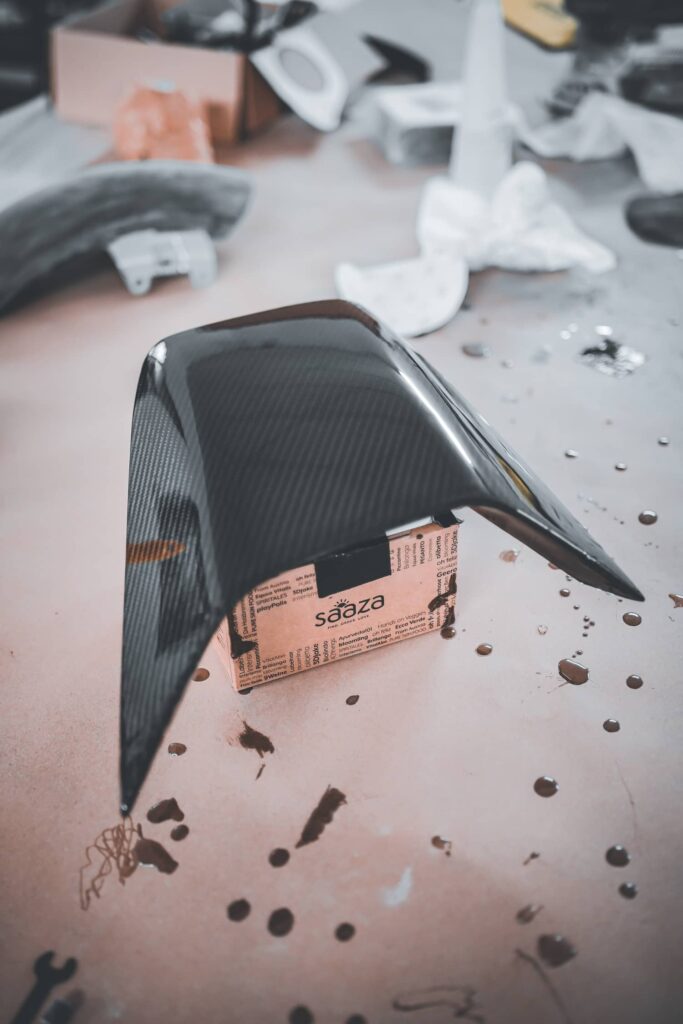
PORSCHE 991.2 GT3 WILL BE EVEN FASTER THANKS TO 3D TECHNOLOGIES
Modern 3D technologies have become indispensable in the development and production of products nowadays. 3D printing and 3D scanning technologies are certainly among the most important in product development. The greatest advantages of modern 3D technologies are:
- Enabling faster and more efficient production of prototypes and products in smaller batches,
- Easily adapting and changing product shapes, which is key to producing products that are constantly changing and improving,
- Reducing production costs and time,
- We produce products and shapes that would otherwise be difficult to implement using traditional methods, which encourages creativity and innovation in the production of new products.
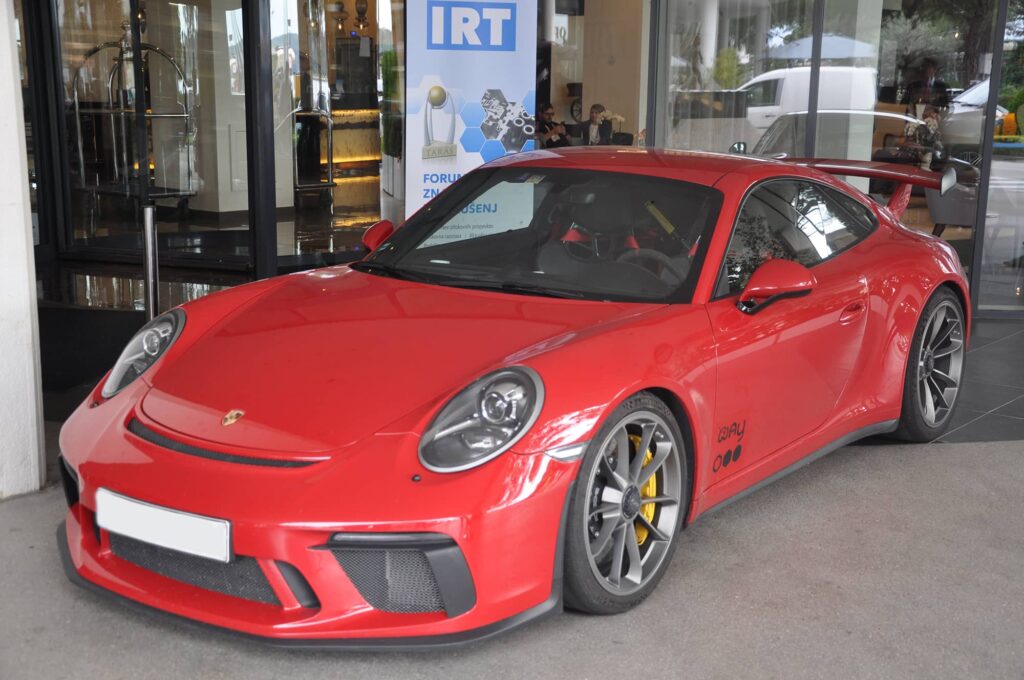
PROJECT PRESENTATION AT THE INDUSTRIAL FORUM (IRT) IN PORTOROSE
Together with Ångström Performance, we presented the entire project and the use of 3D technology on a practical example at the Industrial Forum (IRT) in Portorož as part of a lecture. In our project, due to the use of advanced 3D technologies, the project was carried out quickly and with high quality. We have reduced the time from idea to finished product, which allows us to be much more competitive and deliver a much larger number of projects.
The listeners were very attracted to the project and it garnered a lot of interest. You can watch more in the video below, which was created during visits to the Industrial Forum in Portorose: