Tadej Pogačar has 3D printed components on his bike
New one-piece handlebars, Carbon-Ti chainrings and brake rotors, chrono tyres and, above all, 3D printed components make the road racing bike of the two-time Tour de France winner even more unique. We are, of course, talking about the bike currently ridden by Tadej Pogačar.
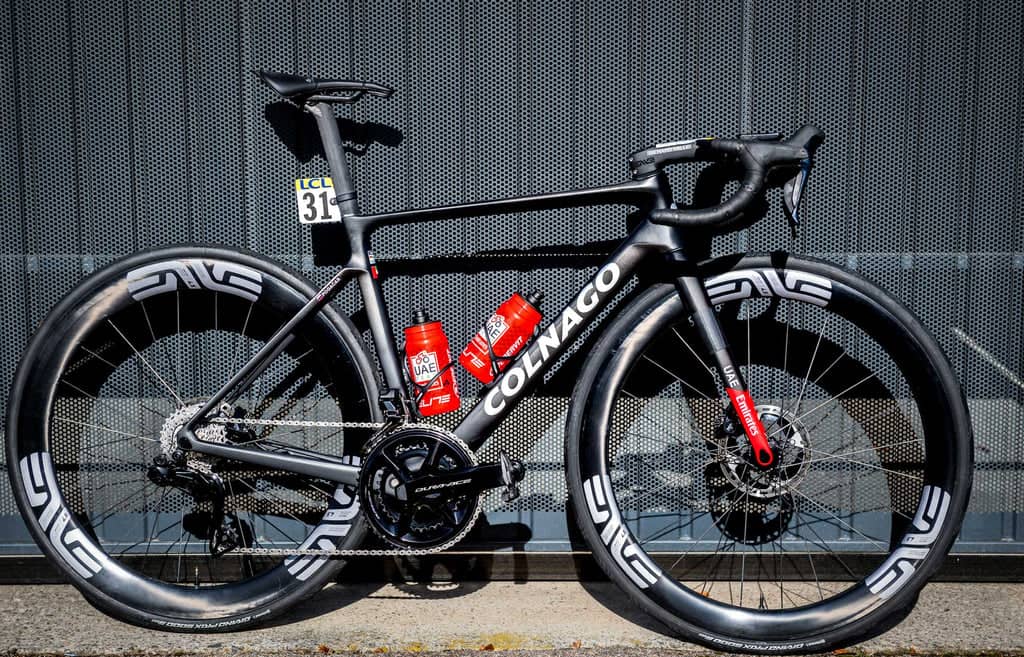
3D PRINTED WHEEL COMPONENTS
Did you know that the professional peloton currently travelling through the French Alps during the Tour de France is increasingly using 3D printed components on their bikes? As a matter of interest, the bike of our star cyclist, Tadejo Pogačar, also has some unique components made with a 3D printer.
Professional riders have been using 3D printed parts for some time now, and 3D printed titanium handlebars were seen on Team Sky bikes in 2015 and at the 2016 Tour de France. In the following years, other 3D printed plastic parts, such as chain catchers, have been seen on various professional bicycles.
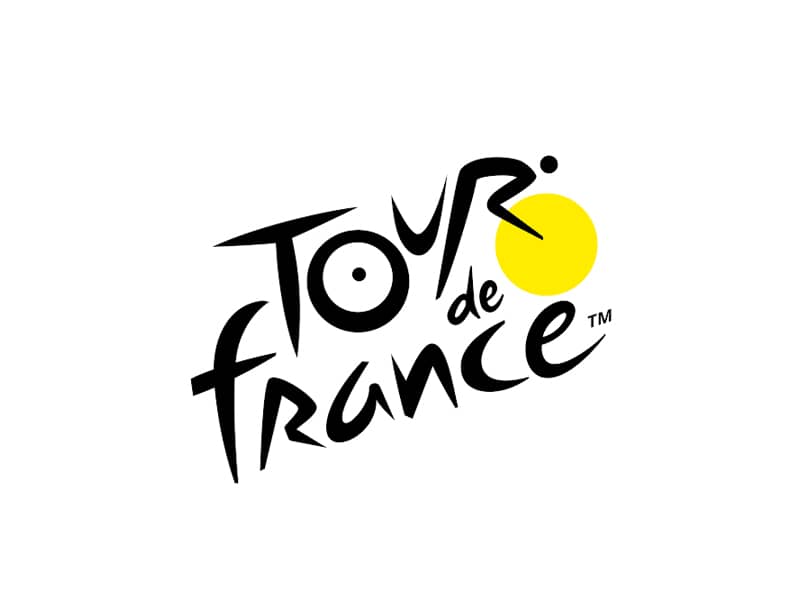
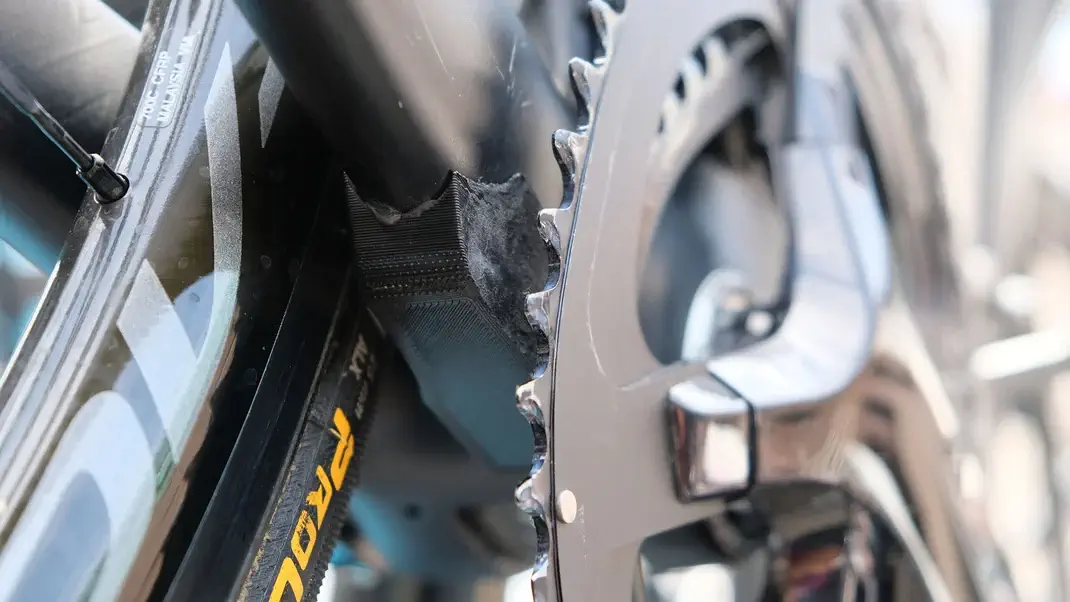
BICYCLE WEIGHT LIMIT
A lot of cycling is about the weight of the equipment, especially the wheels or their rotating components. Bicycles even have a minimum weight limit to ensure safety, because otherwise engineers and mechanics would pluck the bike to the minimum, which is not the most appropriate from the point of view of safe riding. The UCI sets the weight limit for the bike at 6.8 kg. A rider with a bike lighter than this weight is not allowed to compete or is disqualified if this is found after the race. With the advent of disc brakes, taller calipers, etc., even a weight of 6.8 kg is difficult to achieve, so some are already using 3D printed components.
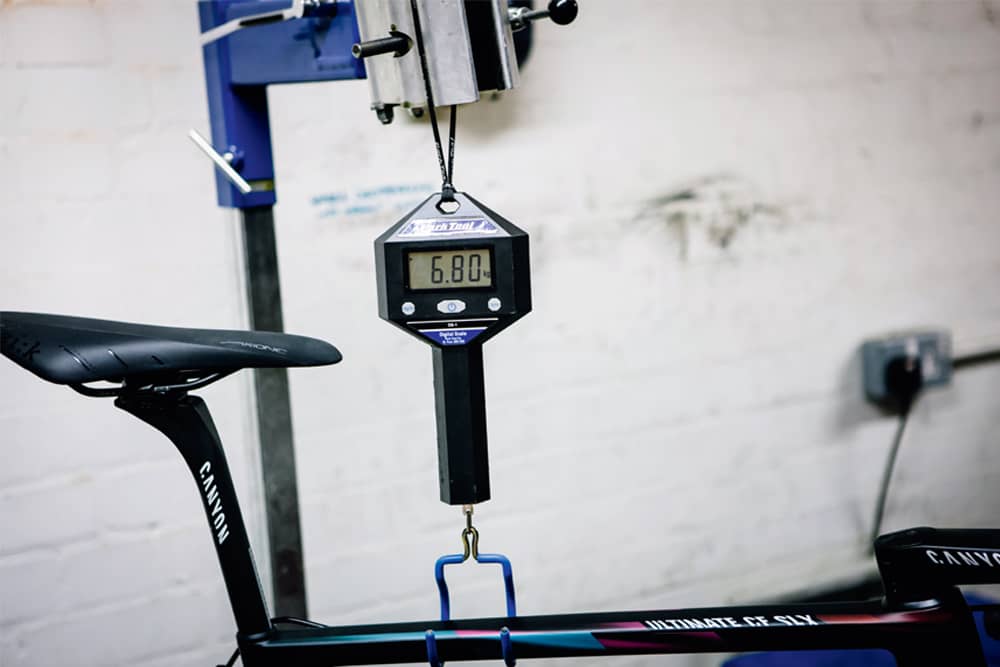
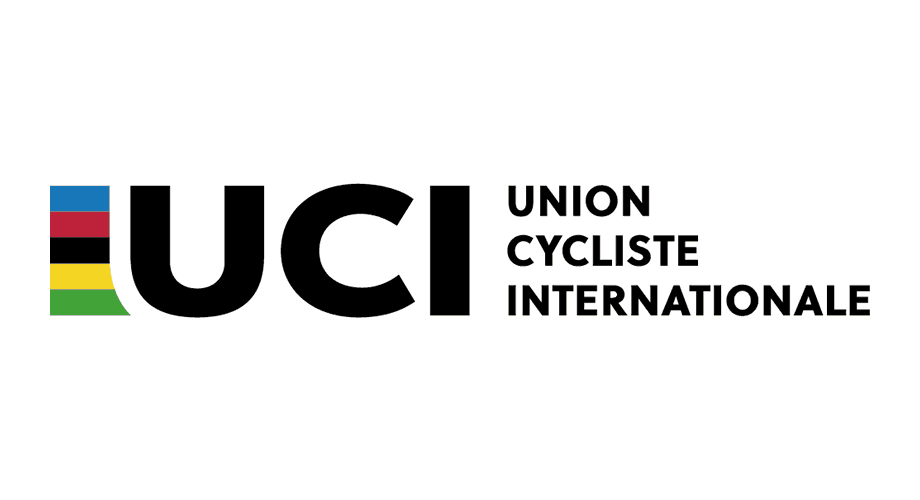
THE IMPORTANCE OF RIGIDITY AND LOW WEIGHT
The components of the bicycle must clearly be optimised as much as possible to provide the necessary stiffness and thus the direct transfer of force from the rider’s legs to the ground. The loss of forces in the material must be kept to a minimum. The focus is on both the static and, even more so, the rotating parts of the wheel. Some components are more difficult to mass-produce because they are still in the development phase, and would be expensive due to their complexity. Here, engineers decided to use 3D printers to make them.
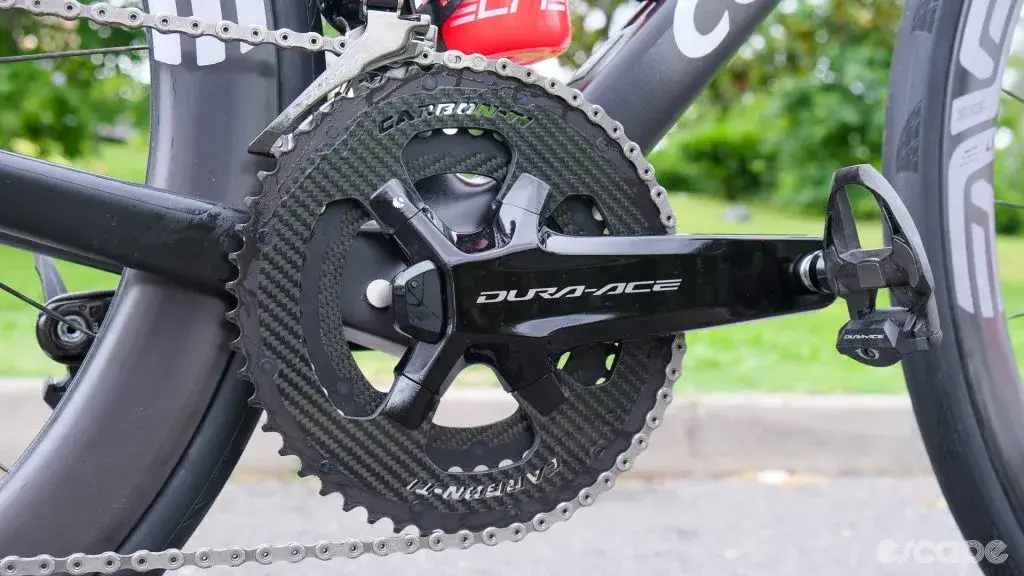
TADEJA POGAČAR'S BICYCLE - MORE 3D PRINTED COMPONENTS
Tadej Pogačar in this year’s Tour de France, where he is currently 2nd. overall, rides a Colnago V4RS bike. The mechanics have also worked with engineers to equip it with some 3D-printed components. Why? Some components are very specific and require a specific shape, which makes them the easiest to make with a 3D printer. Thanks to advanced materials, components can even have a better structure than if they were made using material removal methods, as they can be, say, reinforced in a specific direction.
1. COVER OVER THE STEERING BEARING
The cover over the rudder bearing, which is located under the rudder bracket, is made of carbon reinforced with titanium. It is a fully 3D printed piece, optimised for aerodynamics. It fills the hole between the handlebar mount and the frame, ensuring optimal airflow.
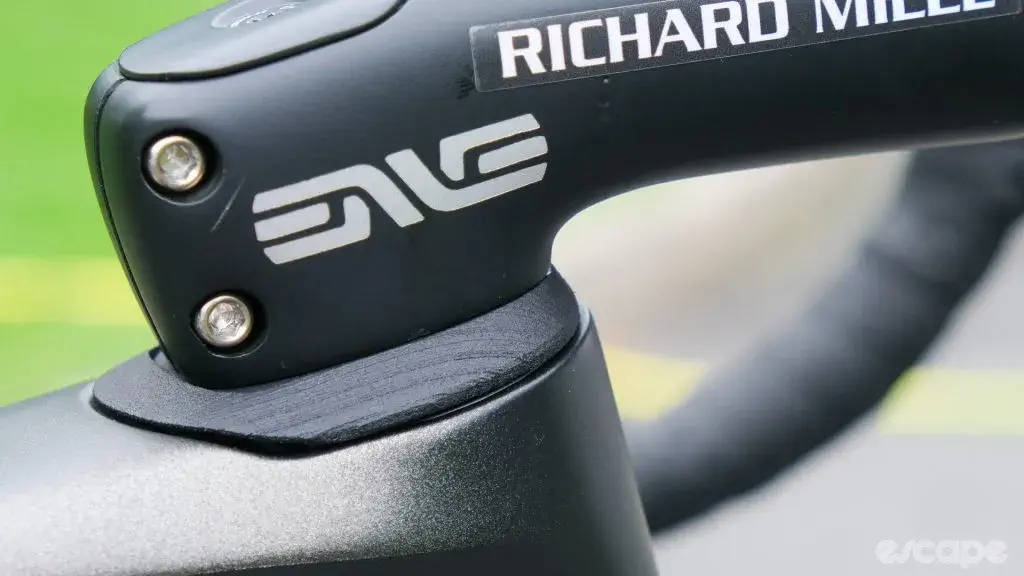
2. NUMBER HOLDER
Cyclists must also have their number on their bike. For the carrier, the UAE team decided to make a special one for their riders. Tadej Pogačar has a unique seat support, which is made in the shape of the letter D. Because of the non-standard seat support, the support had to be adapted. This was of course no problem, as it was simply drawn in the software and the CAD model 3D printed. The result is an ultra-light number holder.
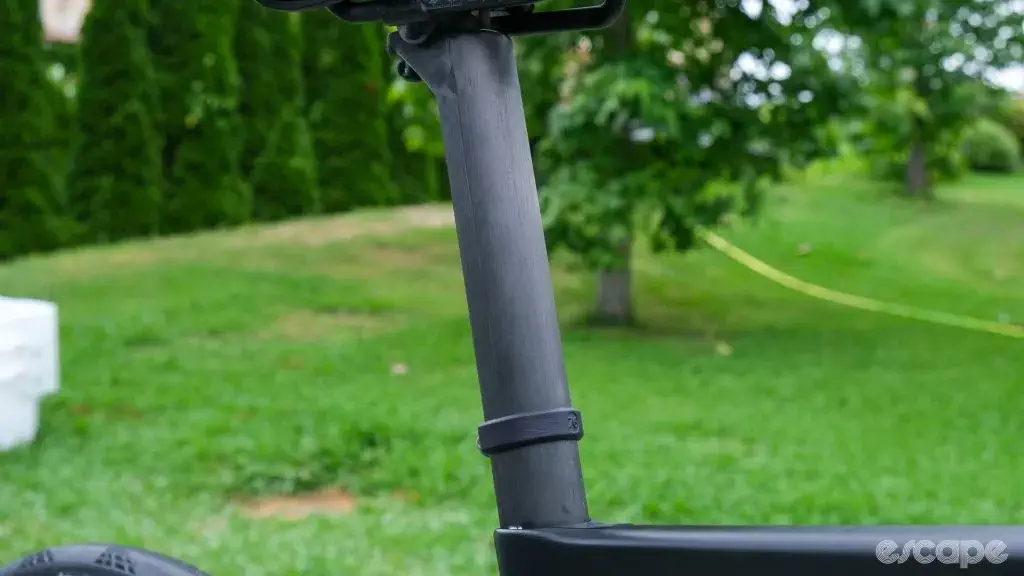
3. CAPS FOR THE SCREWS ON THE CRANK
3D printed bolt covers ensure a smooth transition between crankset and sprocket. As in the case of the cover between the handlebar mount and the frame, aerodynamics are optimised. Each cap is reported to weigh only 2.3 g.
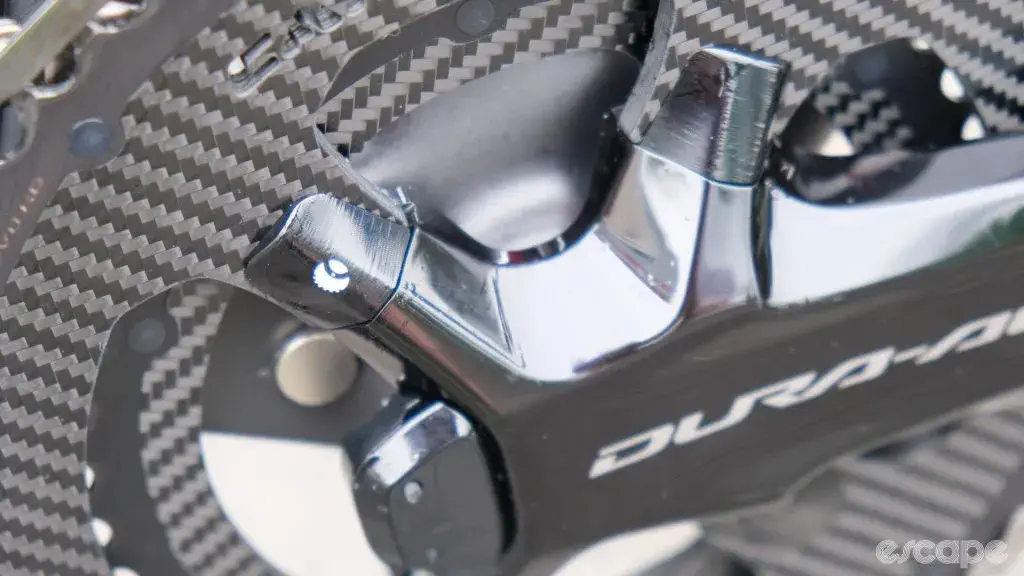
THE FEASIBILITY OF 3D PRINTED COMPONENTS ON A BICYCLE
As mentioned before, in cycling, the main piece of equipment – the bike – has a big influence on the result, assuming of course that the rider is in top shape. If we take the Tour de France as an example, the gaps are measured in per mille, so equipment can also be crucial. By optimising the equipment, a team or an individual can not only gain, but save some valuable energy, which can later be used to make a decisive attack and perhaps even win a race of this magnitude. Lightweight and rigid components are essential, and the latter are most easily produced using a 3D printer due to their complexity.
We are confident that the number of 3D printed components on the wheels of professionals will increase over the years. Of course, any cycling enthusiast with 3D printing skills can play around a bit and maybe produce a useful component. The possibilities with 3D printers are endless.
- Carbon Fiber
MakerBot Nylon Carbon Fiber (PA-CF) 1,75 mm Black 0,5 kg
151,20 €Original price was: 151,20 €.142,12 €Current price is: 142,12 €. Add to cart - Sale!
Out of stock
Carbon FiberFlashForge PLA-CF 1.75 mm Black
56,70 €Original price was: 56,70 €.46,49 €Current price is: 46,49 €. Read more - Carbon Fiber
FlashForge PA-CF 1.75 mm Black
89,70 €Original price was: 89,70 €.79,83 €Current price is: 79,83 €. Add to cart - Carbon Fiber
FlashForge PETG-CF 1.75 mm Black
56,70 €Original price was: 56,70 €.46,49 €Current price is: 46,49 €. Add to cart